Nissan Sentra Service Manual: Chassis and body maintenance
In-cabin microfilter
In-cabin microfilter : removal and installation
REMOVAL
- Remove the in-cabin microfilter cover.
CAUTION:
Before removing the in-cabin microfilter cover, let the vehicle rest
for at least 30 minutes.
- Release the filter cover tab (A), then pull the bottom of the in-cabin
microfilter cover outwards.
- Pull down the in-cabin microfilter cover to disengage the hook at the
top, then remove the in-cabin microfilter
cover.
- Remove the in-cabin microfilter.
INSTALLATION
Installation is in the reverse order of removal.
CAUTION:
After installation, check that the in-cabin microfilter cover is
securely fastened to the heating and cooling
unit assembly.
Exhaust system
Exhaust system : checking exhaust system
Check the exhaust pipes, muffler, and mounting components for
incorrect attachment, leaks, cracks, damage, or deterioration.
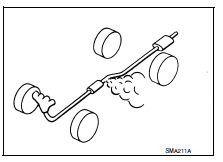
M/t oil
M/T OIL : Inspection
OIL LEAKAGE
Make sure that gear oil is not leaking from transaxle or around it.
OIL LEVEL
- Remove filler plug (1) and gasket from transaxle case.
- Check the oil level from filler plug mounting hole as shown.
CAUTION:
Do not start engine while checking oil level.
- Set a gasket on filler plug and then install it to transaxle case.
CAUTION:
Do not reuse gasket.
- Tighten filler plug to the specified torque. Refer to TM-30,
"Exploded View".
CAUTION:
Do not overtighten the filler plug as this could cause the
transaxle case to crack.
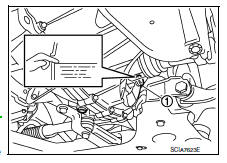
M/T OIL : Draining .
- Start engine and let it run to warm up transaxle.
- Stop engine. Remove drain plug (1) and gasket, using a suitable
tool and then drain gear oil.
- Set a gasket on drain plug and install it to clutch housing, using
a suitable tool.
CAUTION:
Do not reuse gasket.
- Tighten drain plug to the specified torque. Refer to TM-30,
"Exploded View".
CAUTION:
Do not overtighten the filler plug as this could cause the
transaxle case to crack.
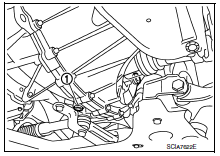
M/T OIL : Refilling
- Remove filler plug (1) and gasket from transaxle case.
- Fill with new gear oil until oil level reaches the specified limit at
filler plug mounting hole as shown.
Oil grade and
viscosity
: Refer to MA-11, "Fluids and Lubricants".
Oil capacity : Refer to MA-11, "Fluids and Lubricants".
- After refilling gear oil, check the oil level. Refer to MA-22, "M/T
OIL : Inspection".
- Set a gasket on filler plug and then install it to transaxle case.
CAUTION:
Do not reuse gasket.
- Tighten filler plug to the specified torque. Refer to TM-30, "Exploded
View".
CAUTION:
Do not overtighten the filler plug as this could cause the transaxle
case to crack.
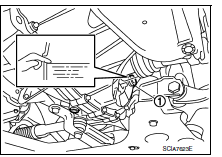
Cvt fluid
CVT FLUID : Inspection
FLUID LEAKAGE
- Check transaxle surrounding area (oil seal and plug etc.) for fluid
leakage.
- If anything is found, repair or replace damaged parts and adjust
CVT fluid level. Refer to MA-25, "CVT FLUID : Adjustment".
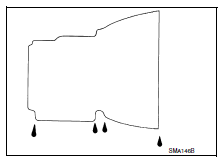
CVT FLUID : Replacement
Recommended CVT fluid and fluid capacity : Refer to TM-288,
"General Specification".
CAUTION:
- Use only recommended CVT fluid. Using transmission fluid other
than recommended CVT fluid will
damage the CVT, which is not covered by the warranty.
- Always use shop paper. Do not use shop cloth.
- Replace a drain plug gasket with new ones at the final stage of
the operation when installing.
- Use caution when looking into the drain hole as there is a risk of
dripping fluid entering the eye.
- After replacement, always perform CVT fluid leakage check.
- Select “Data Monitor” in “TRANSMISSION” using CONSULT.
- Select “FLUID TEMP” and confirm that the CVT fluid temperature is 40°C
(104В°F) or less.
- Check that the selector lever is in the “P” position, then completely
engage the parking brake.
- Lift up the vehicle.
- Remove the drain plug and overflow tube and drain the CVT fluid from the
oil pan. Refer to TM-266,
"Exploded View".
- Install the charging pipe set (KV311039S0) (A) into the drain
hole.
CAUTION:
Tighten the charging pipe by hand.
- Install the ATF changer hose (B) to the charging pipe.
CAUTION:
Press the ATF changer hose all the way onto the charging
pipe until it stops.
- Fill approximately 3 liter (2-5/8 lmp qt) of the CVT fluid.
- Remove the ATF changer hose and charging pipe, then install
the drain plug.
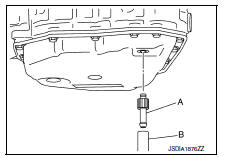
NOTE:
Perform this work quickly because CVT fluid leaks.
- Lift down the vehicle.
- Start the engine.
- While depressing the brake pedal, shift the selector lever to the entire
position from “P” to “L”, and shift it
to the “P” position.
NOTE:
Hold the lever at each position for 5 seconds.
Check that the CONSULT “Data monitor” in “FLUID TEMP” is 35°C (95°F) to 45°C
(113В°F).
- Stop the engine.
- Lift up the vehicle.
- Remove the drain plug, and then drain CVT fluid from oil pan.
- Repeat steps 6 to 16 (one time).
- Install the overflow tube. Refer to TM-266, "Exploded View".
CAUTION:
Be sure to tighten to the specified torque. If it is not tightened to
the specified torque, the tube may
be damaged.
- Install the charging pipe set (KV311039S0) (A) into the drain
hole.
CAUTION:
Tighten the charging pipe by hand.
- Install the ATF changer hose (B) to the charging pipe.
CAUTION:
Press the ATF changer hose all the way onto the charging
pipe until it stops.
- Fill approximately 3 liter (2-5/8 lmp qt) of the CVT fluid.
- Remove the ATF changer hose and charging pipe, then install
the drain plug.
NOTE:
Perform this work quickly because CVT fluid leaks.
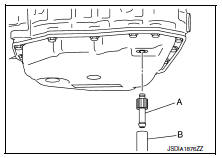
- Lift down the vehicle.
- Start the engine.
- While depressing the brake pedal, shift the selector lever to the entire
position from “P” to “L”, and shift it
to the “P” position.
NOTE:
Hold the lever at each position for 5 seconds.
- Check that the CONSULT “Data monitor” in “FLUID TEMP” is 35°C (95°F) to
45В°C (113В°F).
- Lift up the vehicle.
- Remove the drain plug and confirm that the CVT fluid is drained from the
overflow tube.
CAUTION:
Perform this work with the vehicle idling.
NOTE:
If the CVT fluid is not drained, refer to “Adjustment” and refill with the
CVT fluid.
- When the flow of CVT fluid slows to a drip, tighten the drain plug to
the specified torque. Refer to TM-266,
"Exploded View".
CAUTION:
Do not reuse drain plug gasket.
- Lift down the vehicle.
- Select “Work Support” in “TRANSMISSION” using CONSULT.
- Select “CONFORM CVTF DETERIORTN”.
- Touch “Erase”.
- Stop the engine.
CVT FLUID : Adjustment
Recommended CVT fluid and fluid capacity : Refer to TM-288,
"General Specification".
CAUTION:
- Use only recommended CVT fluid. Using transmission fluid other
than recommended CVT fluid will
damage the CVT, which is not covered by the warranty.
- During adjustment of the CVT fluid level, check CONSULT so that
the oil temperature may be maintained
from 35 to 45В°C (95 to 113В°F).
- Use caution when looking into the drain hole as there is a risk of
dripping fluid entering the eye.
- Check that the selector lever is in the “P” position, then completely
engage the parking brake.
- Start the engine
- Adjust the CVT fluid temperature to be approximately 40В°C (104В°F).
NOTE:
The CVT fluid is largely affected by temperature. Therefore be sure to use
CONSULT and check the
“FLUID TEMP” under “TRANSMISSION” in “Data Monitor” while adjusting.
- While depressing the brake pedal, shift the selector lever to the entire
position from “P” to “L”, and shift it
to the “P” position.
NOTE:
Hold the lever at each position for 5 seconds.
- Lift up the vehicle
- Check that there is no CVT fluid leakage.
- Remove the drain plug. Refer to TM-266, "Exploded View".
- Install the charging pipe set (KV311039S0) (A) into the drain
plug hole.
CAUTION:
Tighten the charging pipe by hand.
- Install the ATF changer hose (B) to the charging pipe.
CAUTION:
Press the ATF changer hose all the way onto the charging
pipe until it stops.
- Fill approximately 0.5 liter (1/2 lmp qt) of the CVT fluid.
- Remove the ATF changer hose from the charging pipe, and
check that the CVT fluid drains out from the charging pipe. If it
does not drain out, perform charging again.
CAUTION:
Perform this work with the vehicle idling.
- When the flow of CVT fluid slows to a drip, remove the charging pipe
from the oil pan.
- Tighten the drain plug to the specified torque. Refer to TM-266,
"Exploded View".
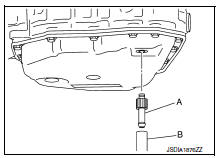
CAUTION:
Do not reuse drain plug gasket.
- Lift down the vehicle.
- Stop the engine.
Wheels
Wheels : inspection
ALUMINUM WHEEL
- Check tires for wear and improper inflation.
- Check wheels for deformation, cracks and other damage. If deformed,
remove wheel and check wheel
runout.
- Remove tire from aluminum wheel and mount wheel on a balancer machine.
- Set dial indicator as shown.
- Check runout, if runout value exceeds the limit, replace aluminum
wheel.
Limit
Lateral Deflection (A) Refer to WT-54, "Road Wheel".
Radial Deflection (B) Refer to WT-54, "Road Wheel".
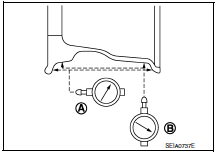
STEEL WHEEL
- Check tires for wear and improper inflation.
- Check wheels for deformation, cracks and other damage. If deformed,
remove wheel and check wheel
runout.
- Remove tire from steel wheel and mount wheel on a balancer machine.
- Set two dial indicators as shown.
- Set each dial indicator to "0".
- Rotate wheel and check dial indicators at several points around
the circumference of the wheel.
- Calculate runout at each point as shown below.
Lateral deflection (A) = (W+X)/2
Radial deflection (B) = (Y+Z)/2
- Select maximum positive runout value and the maximum negative
value.
Add the two values to determine total runout.
In case a positive or negative value is not available, use the
maximum value (negative or positive) for total runout.
If the total runout value exceeds the limit, replace steel wheel.
Limit
Lateral Deflection (A) Refer to WT-54, "Road Wheel".
Radial Deflection (B) Refer to WT-54, "Road Wheel".
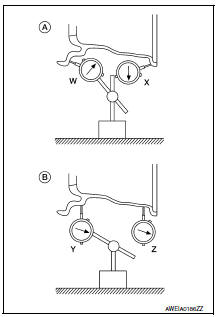
Wheels : adjustment
BALANCING WHEELS (ADHESIVE WEIGHT TYPE)
Preparation Before Adjustment
Remove inner and outer balance weights from the road wheel. Using releasing
agent, remove double-faced
adhesive tape from the road wheel.
CAUTION:
- Be careful not scratch the road wheel during removal.
- After removing double-faced adhesive tape, wipe clean all traces
of releasing agent from the road
wheel.
Wheel Balance Adjustment
- Set road wheel on balancer machine using the center hole as a guide.
Start the balancer machine.
- For balancer machines that only have a clip-on (rim flange) weight mode
setting, follow this step to calculate
the correct size adhesive weight to use. When inner and outer imbalance
values are shown on the
balancer machine indicator, multiply outer imbalance value by 5/3 (1.67) to
determine balance weight that
should be used. Select the outer balance weight with a value closest to the
calculated value above and
install in to the designated outer position of, or at the designated angle
in relation to the road wheel.
- Indicated imbalance value × 5/3 (1.67) = balance weight to be
installed
Calculation example:
23 g (0.81 oz) × 5/3 (1.67) = 38.33 g (1.35 oz) ⇒ 40 g (1.41 oz)
balance weight (closer to calculated balance weight value)
NOTE:
Note that balance weight value must be closer to the calculated
balance weight value.
Example:
37.4 ⇒ 35 g (1.23 oz)
37.5 ⇒ 40 g (1.41 oz)
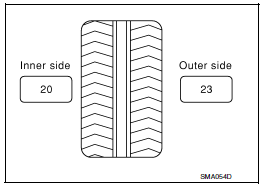
- Install balance weight in the position shown.
CAUTION:
- Do not install the inner balance weight before installing
the outer balance weight.
- Before installing the balance weight, be sure to clean the
mating surface of the road wheel.
- When installing balance weight (1) to road wheel, set it into the
grooved area (A) on the inner wall of the road wheel as shown
so that the balance weight center (B) is aligned with the balancer
machine indication position (angle) (C).
CAUTION:
- Always use Genuine NISSAN adhesive balance weights.
- Balance weights are non-reusable; always replace with
new ones.
- Do not install more than three sheets of balance weight.
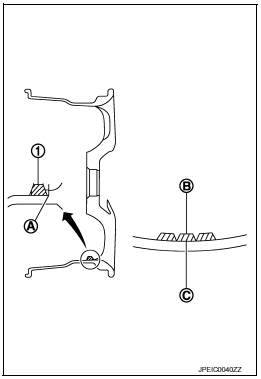
CAUTION:
- Always use Genuine NISSAN adhesive balance weights.
- Balance weights are non-reusable; always replace with
new ones.
- Do not install more than three sheets of balance weight.
- If calculated balance weight value exceeds 50 g (1.76 oz), install
two balance weight sheets in line with each other as shown.
CAUTION:
Do not install one balance weight sheet on top of another.
- Start balancer machine again.
- Install balance weight on inner side of road wheel in the balancer
machine indication position (angle).
CAUTION:
Do not install more than two balance weights.
- Start balancer machine. Make sure that inner and outer residual
imbalance values are 5 g (0.18 oz) each or below.
- If either residual imbalance value exceeds 5 g (0.18 oz), repeat
installation procedures.
Allowable imbalance Refer to WT-54, "Road Wheel".
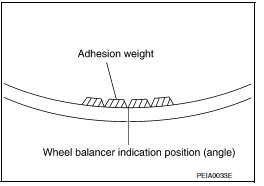
Tire rotation
Caution:
- Do not include the t-type spare tire when rotating the tires.
- When installing wheels, tighten them diagonally by dividing
the work two to three times in order to prevent the wheels
from developing any distortion.
- Be careful not to tighten wheel nut at torque exceeding the
criteria for preventing strain of disc rotor.
- Use nissan genuine wheel nuts for aluminum wheels.
Wheel nut tightening torque refer to wt-54, "road wheel".
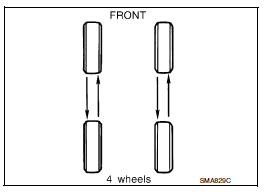
Brake fluid level and leaks
Brake fluid level and leaks : inspection
Brake fluid level
- Make sure that the brake fluid level in the reservoir tank is between
the max and min lines.
- Visually check around the reservoir tank for brake fluid leakage.
- If the brake fluid level is excessively low, check the brake system
for leakage.
- If brake warning lamp remains illuminated after parking brake
pedal is released, check the brake system for brake fluid leakage.
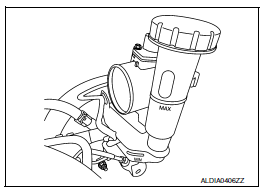
Brake line
- Check brake line (tubes and hoses) for cracks, deterioration or other
damage. Replace any damaged
parts.
- Check for brake fluid leakage by depressing brake pedal under
a force of 785 n (80 kg-f, 177 lb-ft) for approximately 5 seconds
while engine is running.
Caution:
If brake fluid leakage occurs around joints, retighten or
replace damaged parts as necessary.
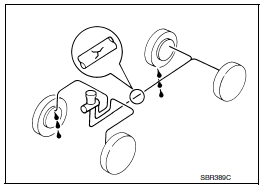
Brake lines and cables
BRAKE LINES AND CABLES : Inspection
- Check brake fluid lines and parking brake cables for improper
attachment, leaks, chafing, abrasions, deterioration, etc.
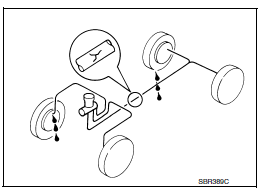
Brake fluid
BRAKE FLUID : Drain and Refill
Caution:
- Do not spill or splash brake fluid on painted surfaces. Brake
fluid may damage paint. If brake fluid is
splashed on painted areas, wash it away with water immediately.
- Prior to repair, turn the ignition switch off, disconnect the abs
actuator and electric unit (control
unit) connector or negative battery terminal. Refer to pg-50, "exploded view".
- Refill brake system with new brake fluid. Refer to ma-11, "fluids
and lubricants".
- Do not reuse drained brake fluid.
Draining
- Turn ignition switch OFF and disconnect ABS actuator and electric unit (control
unit) connector or negative
battery terminal. Refer to PG-50, "Exploded View".
- Connect a vinyl tube to bleeder valve
- Depress brake pedal, loosen bleeder valve, and gradually
remove brake fluid.
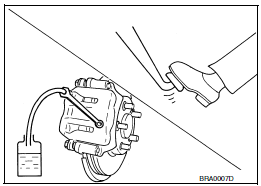
Refilling
- Make sure no foreign material exists in the reservoir and refill with
new brake fluid.
Caution:
Do not reuse drained brake fluid.
- Refill the brake system as follows:
- Depress the brake pedal.
- Loosen bleeder valve.
- Slowly depress brake pedal to 2/3 of the brake pedal full stroke.
- Tighten bleeder valve.
- Release brake pedal.
Repeat this operation at intervals of two or three seconds until all old
brake fluid is discharged. Add new
brake fluid to master cylinder reservoir sub tank frequently.
Caution:
Do not allow master cylinder reservoir to empty as this may cause
damage to master cylinder
internal components.
- Bleed the air out of the brake hydraulic system. Refer to br-17, "bleeding
brake system".
Front disc brake
Front disc brake : inspection
Pad wear
Check brake pad thickness from an inspection hole on caliper body.
Check using a scale if necessary.
Wear limit thickness : refer to br-55, "front disc
brake".
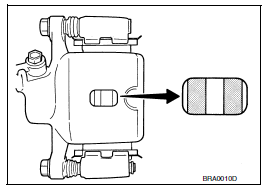
Front disc brake : inspection
Appearance
Check surface of disc rotor for uneven wear, cracks or damage. Replace if any
abnormal conditions exist.
Runout
- Check the wheel bearing axial end play before the inspection. Refer to
fax-6, "inspection".
- Secure the disc rotor to the wheel hub and bearing assembly
with wheel nuts at two wheel nut locations.
- Inspect the runout with a dial gauge, measured at 10 mm (0.39
In) inside the disc edge.
Runout : refer to br-55, "front disc brake".
- Find the installation position with a minimum runout by shifting
the disc rotor-to-wheel hub and bearing assembly installation
position by one hole at a time if the runout exceeds the limit
value.
- Refinish the disc rotor if the runout is outside the limit even after
performing the above operation. When refinishing, use tool.
Tool number : 38-pfm90.5 ( — )
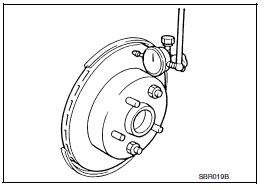
Thickness
Check the thickness of the disc rotor using a micrometer. Replace
the disc rotor if the thickness is below the wear limit.
Wear thickness : refer to br-55, "front disc
brake".
Thickness variation : refer to br-55, "front disc
brake".
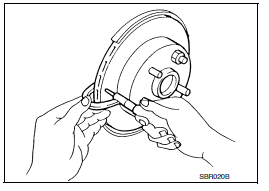
Front disc brake : brake burnishing
Caution:
- Burnish contact surfaces between brake pads and disc rotor
according to the following procedure
after refinishing the disc rotor, replacing brake pads or if a soft pedal
occurs at very low mileage.
- Be careful of vehicle speed. Brakes do not operate firmly/securely
until pads and disc rotor are
securely seated.
- Only perform this procedure under safe road and traffic
conditions. Use extreme caution.
- Drive the vehicle on straight, flat road.
- Depress the brake pedal until the vehicle stops.
- Release the brake pedal for a few minutes to allow the brake components
to cool.
- Repeat steps 1 to 3 until pad and disc rotor are securely seated.
Rear drum brake
Rear drum brake : inspection
Inspection
Brake lining
- Check brake lining wear thickness (a). Check using a scale if
necessary.
Lining wear thickness (a) : refer to br-55, "rear
drum brake".
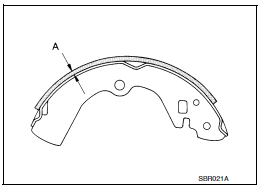
Rear drum brake : inspection
Inspection
Appearance
Check surface of brake drum for uneven wear, cracks and serious damage.
Replace it if necessary. Refer to
br-42, "removal and installation".
Brake drum inner diameter
Check inner diameter (b) of the brake drum using suitable tool.
Brake drum inner diameter (b) : refer to br-55, "rear
drum brake".
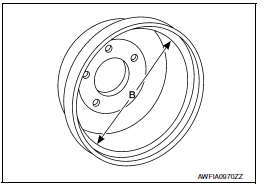
Rear drum brake : brake burnishing
Caution:
- Burnish contact surfaces between brake drum and brake lining
according to the following procedure
after refinishing or replacing brake drum, or if a soft pedal occurs at very
low mileage.
- Be careful of vehicle speed because the brake does not operate
firmly/securely until brake drum and
brake lining are securely fitted.
- Only perform this procedure under safe road and traffic
conditions. Use extreme caution.
- Drive the vehicle on straight, flat road.
- Depress the brake pedal until the vehicle stops.
- Release the brake pedal for a few minutes to allow the brake components
to cool.
- Repeat steps 1 to 3 until pad and disc rotor are securely seated.
Rear disc brake
Rear disc brake : inspection
Pad wear
Check pad thickness from an inspection hole on caliper body. Check
using a scale if necessary.
Wear limit thickness : refer to br-55, "rear disc
brake".
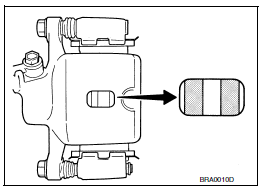
Rear disc brake : inspection
Apperance
Check surface of disc rotor for uneven wear, cracks or damage. Replace if any
abnormal conditions exist.
Runout
- Check the wheel bearing axial end play before the inspection. Refer to
rax-5, "inspection".
- Secure the disc rotor to the wheel hub and bearing assembly
with wheel nuts at two wheel nut locations.
- Inspect the runout with a dial gauge, measured at 10 mm (0.39
In) inside the disc edge.
Runout : refer to br-55, "rear
disc brake".
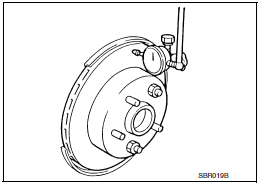
- Find the installation position with a minimum runout by shifting
the disc rotor-to-wheel hub and bearing assembly installation
position by one hole at a time if the runout exceeds the limit
value.
- Refinish the disc rotor if the runout is outside the limit even after
performing the above operation. When
refinishing, use tool.
Tool number : 38-pfm90.5 ( — )
Thickness
Check the thickness of the disc rotor using a micrometer. Replace
the disc rotor if the thickness is below the minimum thickness.
Minimum thickness : refer to br-55, "rear disc
brake".
Thickness variation : refer to br-55, "rear disc
brake".
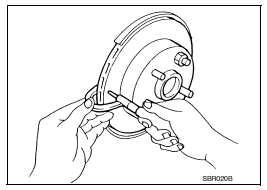
Rear disc brake : brake burnishing
Caution:
- Burnish contact surfaces between brake pads and disc rotor
according to the following procedure
after refinishing the disc rotor, replacing brake pads or if a soft pedal
occurs at very low mileage.
- Be careful of vehicle speed. Brakes do not operate firmly/securely
until pads and disc rotor are
securely seated.
- Only perform this procedure under safe road and traffic
conditions. Use extreme caution.
- Drive the vehicle on straight, flat road.
- Depress the brake pedal until the vehicle stops.
- Release the brake pedal for a few minutes to allow the brake components
to cool.
- Repeat steps 1 to 3 until pad and disc rotor are securely seated.
Steering gear and linkage
Steering gear and linkage : inspection
Inspection after disassembly
Boot
- Check boot for cracks. Replace if any damage is found.
Steering gear assembly housing
- Check steering gear assembly housing for damage and scratches. Replace
if there are any abnormal conditions.
Outer socket and inner socket
- Ball joint swinging torque
- Hook a spring balance to the ball stud and inner socket measuring
point (*) and pull the spring balance. Make sure that the spring balance
reads the specified value when ball stud and inner socket
start to move. Replace outer socket and inner socket if they are
outside the specification.
Tool number : — (j-44372)
Swinging torque : refer to st-19, "power steering
gear".

Ball joint rotating torque
- Make sure that the reading is within the following specified range
using tool (a). Replace outer socket if the reading is outside the
specification.
Tool number (a) : st3127s000 (j-25765-a)
rotating torque : refer to st-19, "power steering
gear".
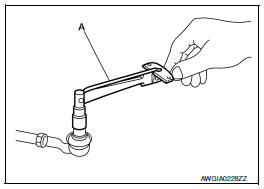
Ball joint axial end play
- Apply an axial load of 490 n (50 kg, 111 lb.) To ball stud. Measuring
the amount of stud movement using a dial gauge, make sure that
the value is within specification. Replace outer socket (a) and
inner socket (b) if the measured value is outside specification.
Axial end play : refer to st-19, "power steering
gear".
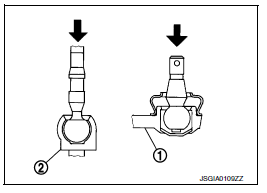
Inspection after installation
- Check if steering wheel turns smoothly when it is turned several times
fully to the end of the left and right.
- Check the steering wheel play, neutral position steering wheel, steering
wheel turning force, and front wheel
turning angle.
- Steering wheel play: Refer to ST-18, "Steering Wheel".
- Neutral position steering wheel, steering wheel turning force, and front
wheel turning angle: refer to st-5,
"inspection".
Axle and suspension parts
Axle and suspension parts : inspection
Check front and rear axle and suspension parts for excessive play,
cracks, wear or other damage.
- Shake each wheel to check for excessive play.
- Check wheel bearings for smooth operation.
- Check axle and suspension nuts and bolts for looseness.
- Check strut (shock absorber) for oil leakage or other damage.
- Check suspension ball joint for grease leakage and ball joint dust
cover for cracks or other damage.
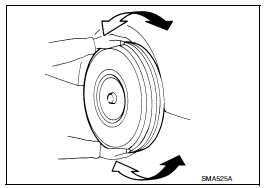
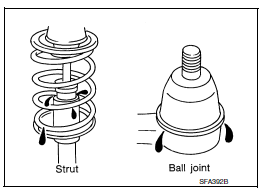
Drive shaft
Drive shaft : inspection
Check the following items, and replace the part if necessary.
- Check drive shaft mounting point and joint for looseness and other
damage.
Caution:
Replace entire drive shaft assembly when noise or vibration occurs from
drive shaft.
- Check boot for cracks and other damage.
Locks, hinges and hood latch
LOCKS, HINGES AND HOOD LATCH : Lubricating
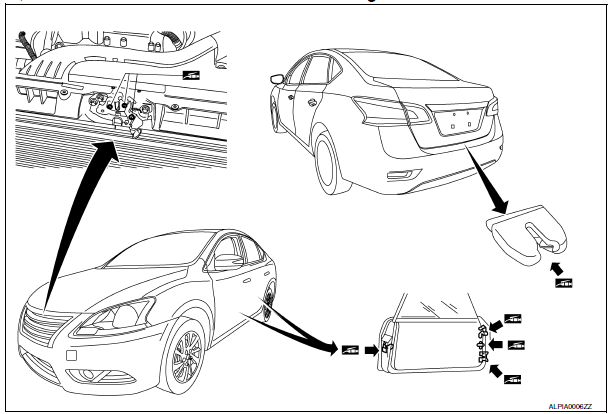
Seat belt, buckles, retractors, anchors
and adjusters
SEAT BELT, BUCKLES, RETRACTORS, ANCHORS
AND ADJUSTERS : Inspection
Caution:
- After any collision, inspect all seat belt assemblies, including
retractors and other attached hardware
(i.E. Anchor bolt, guide rail set). Nissan recommends to replace all seat
belt assemblies in use
during a collision, unless not damaged and properly operating after minor
collision.
Also inspect seat belt assemblies not in use during a collision, and replace
if damaged or improperly
operating.
Seat belt pre-tensioner should be replaced even if the seat belts are not in
use during a frontal collision
where the driver and passenger air bags are deployed.
- If any component of seat belt assembly is questionable, do not
repair.
Replace as seat belt assembly.
- If webbing is cut, frayed, or damaged, replace seat belt assembly.
- Do not oil tongue and buckle.
- Use only a genuine nissan seat belt assembly.
For details, refer to sb-5, "inspection" in the sb section.
- Check anchors for loose mounting.
- Check belts for damage.
- Check retractor for smooth operation.
- Check function of buckles and tongues when buckled and released.
Drive belt
Drive belt : inspection
Alternator
Drive belt auto-tensioner
Crankshaft pulley
A/c compressor
Water pump
Drive belt
Possible use range
New drive belt range
Ndica ...
Other materials:
Compass display (if so equipped)
This unit measures terrestrial magnetism and indicates
heading direction of vehicle.
With the ignition switch in the ON position, press
the button as described in the
chart below
to activate various features of the automatic antiglare
rearview mirror.
For more information about the au ...
During a call
While a call is active, the following options are
available on the screen:
“Handset”
Select this option to switch control of the
phone call over to the handset.
“Mute Mic.”
Select this option to mute the microphone.
Select again to unmute the microphone.
Red phone ( ...
Dlc branch line circuit
Diagnosis Procedure
1.Check connector
Turn the ignition switch off.
Disconnect the battery cable from the negative terminal
Check the terminals and connectors of the data link connector for
damage, bend and loose connection
(connector side and harness side).
Is the inspection result ...
© 2014-2025 Copyright www.nisentra.com