Nissan Sentra Service Manual: Front drive shaft
6M/T
6M/T : Exploded View (LH)
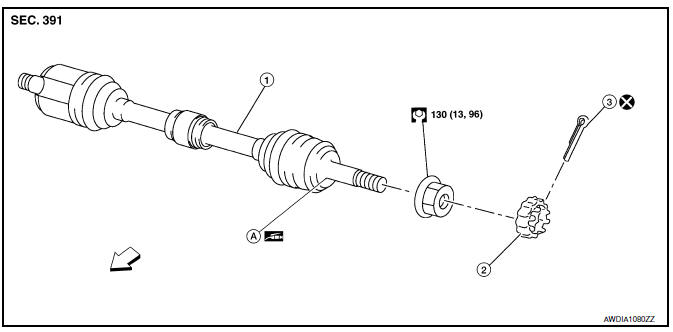
- Front drive shaft
- Nut retainer
- Cotter pin
- Molykote M77
Front
6M/T : Removal and Installation (LH)
NOTE:
When removing components such as hoses, tubes, lines, etc., cap or plug
openings to prevent fluid from spilling.
REMOVAL
- Remove the wheel and tire using power tool. Refer to WT-47, "Exploded
View".
- Drain the M/T fluid. Refer to TM-19, "Draining".
- Remove the brake caliper torque member bolts, leaving the brake hose
attached. Position the brake caliper
aside with wire. Refer to BR-41, "BRAKE CALIPER ASSEMBLY : Removal and
Installation".
CAUTION:
Do not depress the brake pedal while the brake caliper is removed.
- Put alignment marks (A) on the disc brake rotor and on the
wheel hub and bearing. Remove the disc brake rotor.
CAUTION:
Do not drop the disc brake rotor.
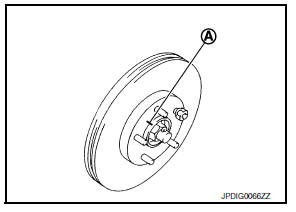
- Remove the wheel sensor bolt. Position the wheel sensor and the wheel
sensor harness aside. Refer to
BRC-106, "FRONT WHEEL SENSOR : Removal and Installation".
- Remove the cotter pin from the drive shaft.
- Remove the nut retainer from the wheel hub lock nut.
- Hold the wheel hub and bearing using Tool (A). Loosen the
wheel hub lock nut.
Tool number (A): KV40104000 ( — )
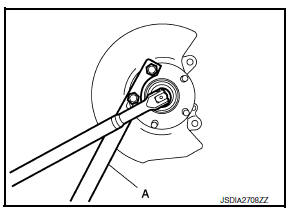
- Using a piece of wood and a suitable tool, tap on the wheel hub
lock nut to disengage the drive shaft from the wheel hub and
bearing.
CAUTION:

NOTE:
Use a suitable puller if the drive shaft cannot be separated from
the wheel hub and bearing even after performing the above procedure.
- Remove the wheel hub lock nut.
- Remove the nut and bolt from the lower ball joint. Disconnect the
steering knuckle from the transverse
link.
- Remove the drive shaft from the wheel hub and bearing.
- Insert the Tool (A) between the shaft and the transaxle. Install a
suitable tool (B) to the Tool (A). Remove the drive shaft from the
transaxle.
CAUTION:
Confirm that the circular clip is attached to the drive shaft.
Tool number (A): KV40107500 ( – )
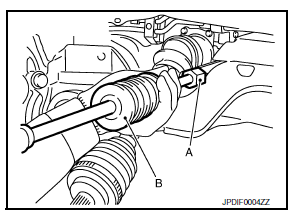
- Remove the differential side oil seal. Refer to TM-20, "Removal and
Installation".
- Inspect the components. Refer to FAX-24, "6M/T : Inspection".
INSTALLATION
Installation is in the reverse order of removal.
TRANSAXLE SIDE
- Install a new differential side oil seal. Refer to TM-20, "Removal and
Installation".
CAUTION:
Do not reuse the differential side oil seal.
- Place Tool (A) onto the differential side oil seal to prevent damage
to the oil seal while inserting the drive shaft. Slide drive shaft sliding
joint and tap with a hammer to install securely.
CAUTION:
Check that circular clip is completely engaged.
Tool number (A): KV38107900 ( – )

- Refill the M/T oil. Refer to TM-19, "Refilling".
- Complete the inspection. Refer to FAX-17, "Inspection".
WHEEL HUB SIDE
- Clean the mating surfaces of the wheel hub lock nut and the wheel hub
and bearing.
CAUTION:
Do not apply lubricating oil to these mating surfaces.
- Clean the mating surfaces of the joint sub-assembly and the wheel
hub and bearing. Apply Molykote M77 lubricant to the surface (A)
of the joint sub-assembly.
CAUTION:
Apply lubricant to cover the entire flat mating surface of the
joint sub-assembly.
NOTE:
Always check with the Parts Department for the latest parts information.
Amount of lubricant : Refer to FAX-49, "Drive
Shaft"
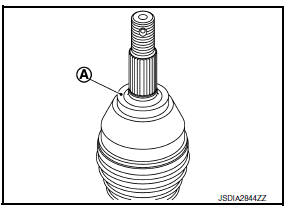
- Hold the wheel hub and bearing using Tool. Tighten the wheel hub lock
nut.
CAUTION:
- Since the drive shaft is assembled by press-fitting, use a torque
wrench to tighten the wheel hub
lock nut. Do not use a power tool.
- Too much torque causes axle noise. Too little torque causes wheel
bearing looseness. Tighten the
wheel hub lock nut to the specification.
Tool number : KV40104000 ( — )
- When installing a the cotter pin (1) and the nut retainer (2),
securely bend the cotter pin to prevent rattles.
CAUTION:
Do not reuse the cotter pin.
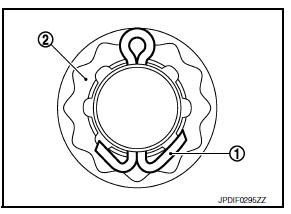
- Align the matching marks (A) on the disc brake rotor and on the
wheel hub and bearing.
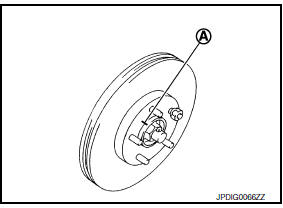
6M/T : Exploded View (RH)
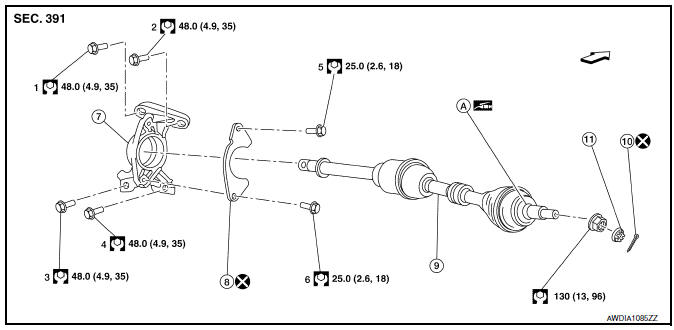
1-6. Tightening order
- Support bearing bracket
- Support bearing bracket plate
- Front drive shaft
- Cotter pin
- Nut retainer
6M/T : Removal and Installation (RH)
REMOVAL
- Remove the wheel and tire using power tool. Refer to WT-47, "Exploded
View".
- Drain the M/T fluid. Refer to TM-19, "Draining".
- Remove the brake caliper torque member bolts, leaving the brake hose
attached. Position the brake caliper
aside with wire. Refer to BR-41, "BRAKE CALIPER ASSEMBLY : Removal and
Installation".
CAUTION:
Do not depress the brake pedal while the brake caliper is removed.
- Put alignment marks (A) on the disc brake rotor and on the
wheel hub and bearing. Remove the disc brake rotor.
CAUTION:
Do not drop the disc brake rotor.
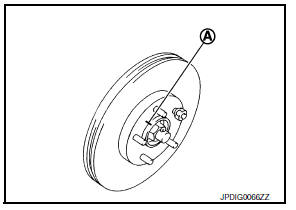
- Remove the wheel sensor bolt. Position the wheel sensor and the wheel
sensor harness aside. Refer to
BRC-106, "FRONT WHEEL SENSOR : Removal and Installation".
- Remove the cotter pin from the drive shaft.
- Remove the nut retainer from the wheel hub lock nut.
- Hold the wheel hub and bearing using Tool (A). Loosen the
wheel hub lock nut.
Tool number (A): KV40104000 ( — )
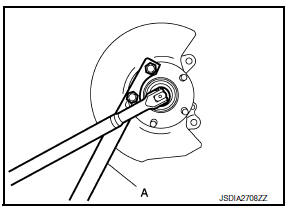
- Using a piece of wood and a suitable tool, tap on the wheel hub
lock nut to disengage the drive shaft from the wheel hub and
bearing.
CAUTION:
NOTE:
Use a suitable puller if the drive shaft cannot be separated from
the wheel hub and bearing even after performing the above procedure.
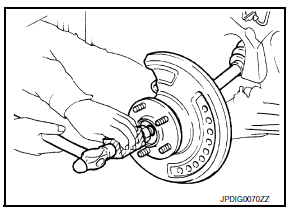
- Remove the wheel hub lock nut.
- Remove the bolts and the support bearing bracket plate.
- Remove the nut and bolt from the lower ball joint. Disconnect the
steering knuckle from the transverse
link.
- Remove the drive shaft from the wheel hub and bearing.
- Remove the drive shaft from the transaxle.
- Remove the differential side oil seal. Refer to TM-20, "Removal and
Installation".
- If necessary, remove the support bearing bracket bolts and the support
bearing bracket.
- Inspect the components. Refer to FAX-24, "6M/T : Inspection".
INSTALLATION
Installation is in the reverse order of removal.
TRANSAXLE SIDE
- Install a new differential side oil seal. Refer to TM-20, "Removal and
Installation".
- When installing the support bearing bracket (1), note the following:
- Tighten the support bearing bracket bolts in 2 stages in the order of
1 to 4 as shown.
- Install the support bearing bracket plate (2) with the notch (A)
upward. Tighten the support bearing bracket plate bolts in 2 stages
in the order of 1 to 2 as shown.
CAUTION:
Do not reuse the support bearing bracket plate.
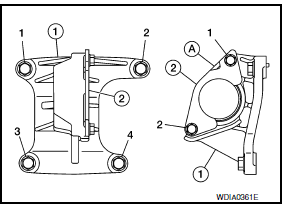
- Place Tool (A) onto the differential side oil seal to prevent damage
to the oil seal while inserting the drive shaft. Slide drive shaft sliding
joint and tap with a hammer to install securely.
Tool number (A): KV38107900 ( – )
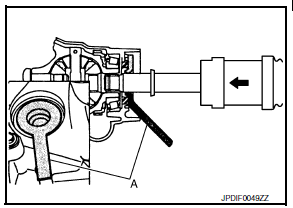
- Refill the M/T oil. Refer to TM-19, "Refilling".
- Complete the inspection. Refer to FAX-17, "Inspection".
WHEEL HUB SIDE
- Clean the mating surfaces of the wheel hub lock nut and the wheel hub
and bearing.
CAUTION:
Do not apply lubricating oil to these mating surfaces.
- Clean the mating surfaces of the joint sub-assembly and the wheel
hub and bearing. Apply Molykote M77 lubricant to the surface (A)
of the joint sub-assembly.
CAUTION:
Apply lubricant to cover the entire flat mating surface of the
joint sub-assembly.
NOTE:
Always check with the Parts Department for the latest parts information.
Amount of lubricant : Refer to FAX-49, "Drive
Shaft"
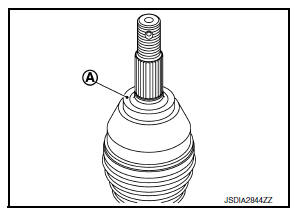
- Hold the wheel hub and bearing using Tool. Tighten the wheel hub lock
nut.
CAUTION:
- Since the drive shaft is assembled by press-fitting, use a torque
wrench to tighten the wheel hub
lock nut. Do not use a power tool.
- Too much torque causes axle noise. Too little torque causes wheel
bearing looseness. Tighten the
wheel hub lock nut to the specification.
Tool number : KV40104000 ( — )
- When installing a the cotter pin (1) and the nut retainer (2),
securely bend the cotter pin to prevent rattles.
CAUTION:
Do not reuse the cotter pin.
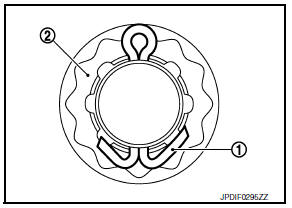
- Align the matching marks (A) on the disc brake rotor and on the
wheel hub and bearing.
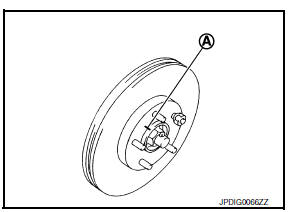
- Complete the inspection. Refer to FAX-17, "Inspection".
6M/T : Inspection
INSPECTION AFTER REMOVAL
Check the following items and replace the part if necessary.
- Move the joint up/down, left/right, and in the axial directions. Check
for motion that is not smooth and for significant
looseness.
- Check the boot for cracks, damage, and grease leaks.
- Check the support bearing bracket for cracks, deformation, and other
damage.
INSPECTION AFTER DISASSEMBLY
Check the following items and replace the part if necessary.
Shaft
Check the shaft for runout, cracks, or other damage. Replace the shaft if
necessary.
Dynamic Damper
Check the dynamic damper for cracks or wear.
Joint Sub-Assembly
Check the following:
- Joint sub-assembly for rough rotation and excessive axial looseness.
- The inside of the joint sub-assembly for entry of foreign material.
- Joint sub-assembly for compression scars, cracks, and fractures inside
of the joint sub-assembly.
Replace the joint sub-assembly if there are any non-standard conditions of
components.
Housing and spider assembly
Replace the housing and spider assembly if there is scratching or wear of the
housing roller contact surface or
the spider roller contact surface.
NOTE:
Replace the housing and spider assembly as a set.
Support Bearing (RH)
Verify the support bearing rolls freely and is free from noise, cracks,
pitting or wear. Replace the support bearing
if there are any non-standard conditions.
Support Bearing Bracket (RH)
Check the support bearing bracket for cracks or damage. Replace the support
bearing bracket if there are any
non-standard conditions.
INSPECTION AFTER INSTALLATION
- Check the wheel sensor harness to be sure the connectors are fully
seated.
- Check the wheel alignment. Refer to FSU-6, "Inspection".
EXCEPT 6M/T
EXCEPT 6M/T : Exploded View
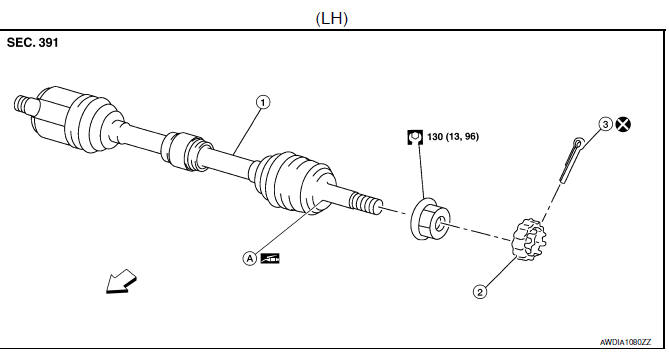
- Front drive shaft
- Nut retainer
- Cotter pin
- Molykote M77
Front
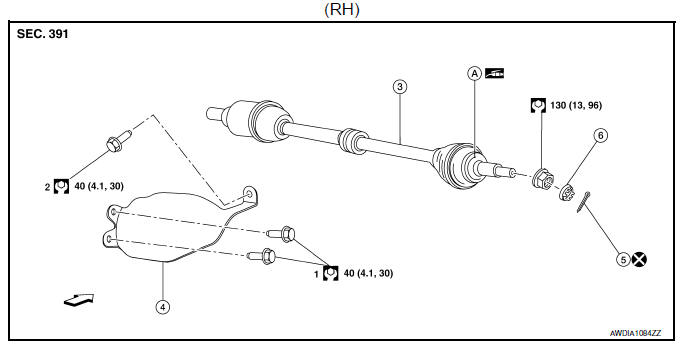
1-2 Tightening order
- Front drive shaft
- Heat shield
- Cotter pin
- Nut retainer
Front
EXCEPT 6M/T : Removal and Installation
NOTE:
When removing components such as hoses, tubes, lines, etc., cap or plug
openings to prevent fluid from spilling.
REMOVAL
- Remove the wheel and tire using power tool. Refer to WT-47, "Exploded
View".
- Remove the brake caliper torque member bolts, leaving the brake hose
attached. Position the brake caliper
aside with wire. Refer to BR-41, "BRAKE CALIPER ASSEMBLY : Removal and
Installation".
CAUTION:
Do not depress the brake pedal while the brake caliper is removed.
- Put alignment marks (A) on the disc brake rotor and on the
wheel hub and bearing. Remove the disc brake rotor.
CAUTION:
Do not drop the disc brake rotor.
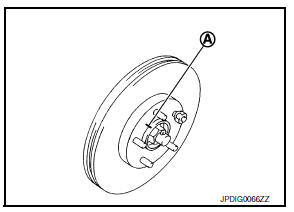
- Remove the wheel sensor bolt. Position the wheel sensor and the wheel
sensor harness aside. Refer to
BRC-106, "FRONT WHEEL SENSOR : Removal and Installation".
- Remove the cotter pin from the drive shaft.
- Remove the nut retainer from the wheel hub lock nut.
- Hold the wheel hub and bearing using Tool (A). Loosen the
wheel hub lock nut.
Tool number (A): KV40104000 ( — )
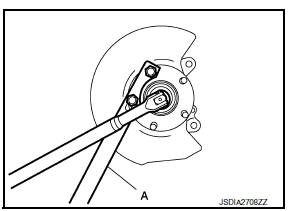
- Using a piece of wood and a suitable tool, tap on the wheel hub
lock nut to disengage the drive shaft from the wheel hub and
bearing.
CAUTION:
NOTE:
Use a suitable puller if the drive shaft cannot be separated from
the wheel hub and bearing even after performing the above procedure.
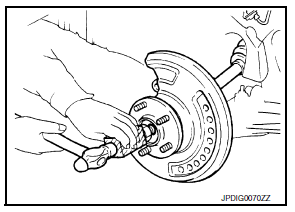
- Remove the wheel hub lock nut.
- Remove the nut and bolt from the lower ball joint. Disconnect the
steering knuckle from the transverse
link.
- Remove the drive shaft from the wheel hub and bearing.
- For the (RH) drive shaft, remove the bolts and the heat shield.
- Insert the Tool (A) between the shaft and the transaxle. Install a
suitable tool (B) to the Tool (A). Remove the drive shaft from the
transaxle.
CAUTION:
Confirm that the circular clip is attached to the drive shaft.
Tool number (A): KV40107500 ( – )
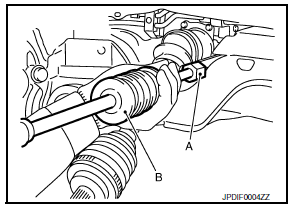
- Remove the differential side oil seal. Refer to TM-271, "Removal and
Installation".
- Inspect the components. Refer to FAX-24, "6M/T : Inspection".
INSTALLATION
Transaxle Side
Installation is in the reverse order of removal.
- Install a new differential side oil seal. Refer to TM-271, "Removal and
Installation".
CAUTION:
Do not reuse the differential side oil seal.
- Place Tool (A) onto the differential side oil seal to prevent damage
to the oil seal while inserting the drive shaft. Slide drive shaft sliding
joint and tap with a hammer to install securely.
CAUTION:
Check that circular clip is completely engaged.
Tool number (A): KV38107900 ( – )
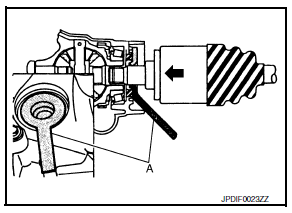
- Check the CVT fluid level. Check the CVT for leaks. Refer to TM-250,
"Inspection".
- Complete the inspection. Refer to FAX-17, "Inspection".
Wheel Hub Side
- Clean the mating surfaces of the wheel hub lock nut and the wheel hub
and bearing.
CAUTION:
Do not apply lubricating oil to these mating surfaces.
- Clean the mating surfaces of the joint sub-assembly and the wheel
hub and bearing. Apply Molykote M77 lubricant to the surface (A)
of the joint sub-assembly.
CAUTION:
Apply lubricant to cover the entire flat mating surface of the
joint sub-assembly.
NOTE:
Always check with the Parts Department for the latest parts information.
Amount of lubricant : Refer to FAX-49, "Drive
Shaft"
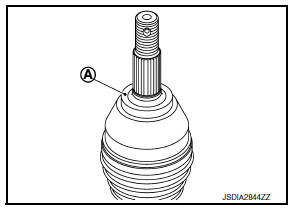
- Hold the wheel hub and bearing using Tool. Tighten the wheel hub lock
nut.
CAUTION:
- Since the drive shaft is assembled by press-fitting, use a torque
wrench to tighten the wheel hub
lock nut. Do not use a power tool.
- Too much torque causes axle noise. Too little torque causes wheel
bearing looseness. Tighten the
wheel hub lock nut to the specification.
Tool number : KV40104000 ( — )
- When installing a the cotter pin (1) and the nut retainer (2),
securely bend the cotter pin to prevent rattles.
CAUTION:
Do not reuse the cotter pin.
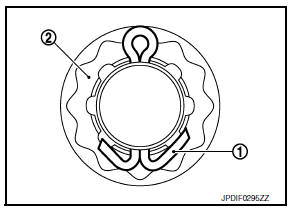
- Align the matching marks (A) on the disc brake rotor and on the
wheel hub and bearing.
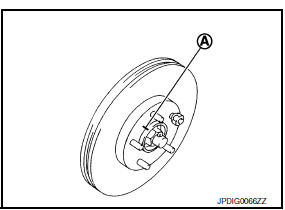
- Complete the inspection. Refer to FAX-17, "Inspection".
EXCEPT 6M/T : Inspection
INSPECTION AFTER REMOVAL
Check the following items and replace the part if necessary.
- Move the joint up/down, left/right, and in the axial directions. Check
for motion that is not smooth and for significant
looseness.
- Check the boot for cracks, damage, and grease leaks.
INSPECTION AFTER DISASSEMBLY
Check the following items and replace the part if necessary.
Shaft
Check the shaft for runout, cracks, or other damage. Replace the shaft if
necessary
Dynamic Damper
Check the dynamic damper for cracks or wear.
Joint Sub-Assembly
Check the following:
- Joint sub-assembly for rough rotation and excessive axial looseness.
- The inside of the joint sub-assembly for entry of foreign material
- Joint sub-assembly for compression scars, cracks, and fractures inside
of the joint sub-assembly.
Replace the joint sub-assembly if there are any non-standard conditions of
components.
Housing and spider assembly
Replace the housing and spider assembly if there is scratching or wear of the
housing roller contact surface or
the spider roller contact surface.
NOTE:
Replace the housing and spider assembly as a set.
INSPECTION AFTER INSTALLATION
- Check the wheel sensor harness to be sure the connectors are fully
seated.
- Check the wheel alignment. Refer to FSU-6, "Inspection".
TRANSAXLE SIDE : Removal and Installation
Remove boot after drive shaft is removed from the vehicle.
For drive shaft removal and installation, follow the instructions bellow.
6M/T: Refer to FAX ...
Other materials:
P0196 EOT Sensor
DTC Logic
DTC DETECTION LOGIC
NOTE:
If DTC P0196 is displayed with DTC P0197 or P0198, first perform the
trouble diagnosis for DTC P0197 or
P0198. Refer to EC-264, "DTC Logic".
DTC No.
CONSULT screen terms
(Trouble diagnosis content)
DTC detecting condition
Possib ...
P0327, P0328 KS
DTC Logic
DTC DETECTION LOGIC
DTC No.
CONSULT screen terms
(Trouble diagnosis content)
DTC detecting condition
Possible cause
P0327
KNOCK SEN/CIRC-B1
(Knock sensor 1 circuit
low bank 1)
An excessively low voltage from the knock sensor
is sent to ECM.
...
A-bag branch line circuit
Diagnosis procedure
Warning:
Always observe the following items for preventing accidental
activation.
Before servicing, turn ignition switch off, disconnect battery
negative terminal, and wait 3 minutes
or more. (To discharge backup capacitor.)
Never use unspecified tester or other me ...
© 2014-2025 Copyright www.nisentra.com