Nissan Sentra Service Manual: Cylinder block
Exploded View
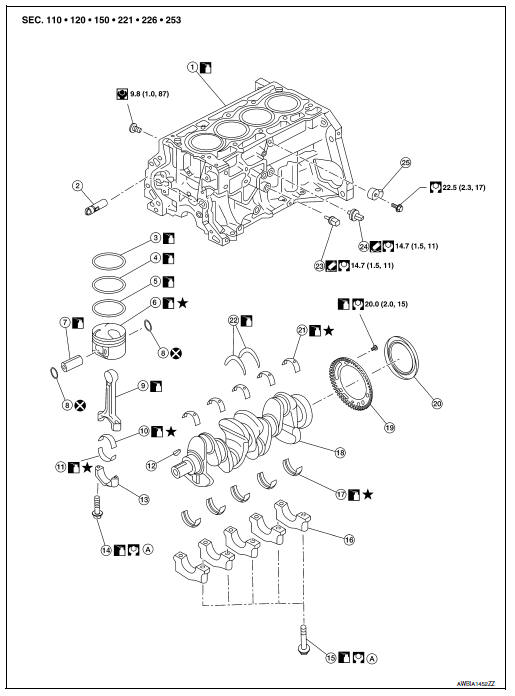
- Cylinder block
- Block heater (for Canada)
- Top ring
- Second ring
- Oil ring
- Piston
- Piston pin
- Snap ring
- Connecting rod
- Connecting rod bearing (upper)
- Connecting rod bearing (lower)
- Crankshaft key
- Connecting rod cap
- Connecting rod cap bolt
- Main bearing cap bolt
- Main bearing cap
- Main bearing (lower)
- Crankshaft
- Signal plate
- Rear oil seal
- Main bearing (upper)
- Thrust bearing
- Oil temperature sensor
- Oil pressure sensor
- Knock sensor
- Refer to INSTALLATION
Disassembly and Assembly
- Remove engine and transaxle assembly from the vehicle. Refer to EM-82,
"M/T : Exploded View" (M/T) or
EM-86, "CVT : Exploded View" (CVT).
- Remove the clutch cover and clutch. Refer to CL-17, "Exploded View".
- Remove the flywheel or drive plate. Refer to EM-90, "Exploded View"
(M/T) or EM-92, "Exploded View"
(CVT).
- Remove pilot converter using Tool.
Tool Number : ST16610001 (J-23907)
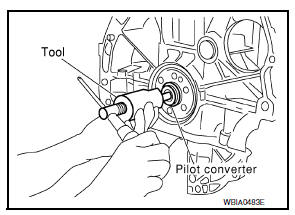
- Remove the rear oil seal. Refer to EM-70, "REAR OIL SEAL : Removal and
Installation".
CAUTION:
Do not damage the crankshaft or cylinder block when removing the rear
oil seal.
- Install engine to engine stand with the following procedure:
- Remove flywheel or drive plate. Refer to EM-90, "Exploded View" (M/T
models) or EM-92, "Exploded
View" (CVT models).
- Remove pilot converter. Refer to EM-92, "Exploded View" (CVT models).
- Lift the engine with a hoist to install it onto widely use engine stand.
CAUTION:
- Use the engine stand that has a load capacity [approximately 135
kg (298 lb) or more] large
enough for supporting the engine weight.
- If the load capacity of stand is not adequate, remove the
following parts beforehand to reduce the potential
risk of overturning stand.
- Intake manifold: Refer to EM-27, "Exploded View".
- Rocker cover: Refer to EM-46, "Exploded View".
NOTE:
The illustration shows an example of widely used engine stand
(A) that can support mating surface of transaxle with flywheel
(M/T models) or drive plate (CVT models) removed.
CAUTION:
Before removing the hanging chains, check the engine
stand is stable and there is no risk of overturning.
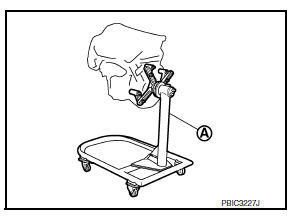
- Drain engine oil. Refer to LU-8, "Draining".
CAUTION:
Be sure to clean drain plug and install with new drain plug washer.
- Drain fluids and lubricants by removing drain plugs (1, 3 and 4)
the cylinder block.
- Tightening torque : Refer to EM-95, "Disassembly and
Assembly".
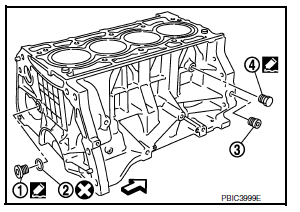
Use Genuine Silicone RTV Sealant, or equivalent. Refer to
GI-21, "Recommended Chemical Products and Sealants".
- Remove the engine harness.
- Remove the oil pan (upper). Refer to EM-33, "Exploded View".
- Remove the water pump. Refer to CO-19, "Exploded View".
- Remove thermostat housing. Refer to CO-21, "Exploded View".
- Remove the water outlet. Refer to CO-24, "Exploded View".
- Remove the cylinder head. Refer to EM-72, "Exploded View".
- Remove knock sensor (2).
CAUTION:
Carefully handle sensor avoiding shocks.
- Remove the oil pressure (3) and oil temp sensor (4).
CAUTION:
Do not reuse O-ring.
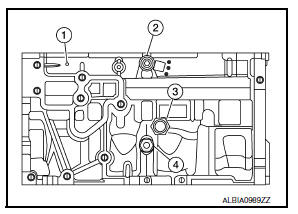
- Remove piston and connecting rod assembly with the following procedure:
- Before removing piston and connecting rod assembly, check the connecting
rod side clearance. Refer to
EM-103, "Inspection".
- Position crankshaft pin corresponding to connecting rod to be removed
onto the bottom dead center.
- Remove connecting rod cap. Number connecting rod caps so they can be
assembled in the same position
and direction.
- Using a hammer handle or similar tool, push piston and connecting
rod assembly out to the cylinder head side.
CAUTION:
- Do not damage matching surface with connecting rod
cap.
- Do not damage the cylinder wall and crankshaft pin,
resulting from an interference of the connecting rod big
end.
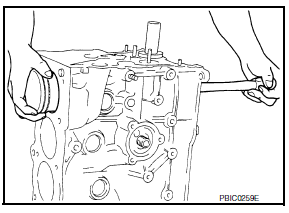
- Remove connecting rod bearings.
CAUTION:
When removing them, note the installation position. Keep them in the
correct order.
- Remove piston rings from piston.
- Before removing piston rings, check the piston ring side clearance.
Refer to EM-103, "Inspection".
- Remove piston rings using suitable tool (A).
CAUTION:
- When removing piston rings, be careful not to damage
the piston.
- Do not damage piston rings by expanding them excessively.
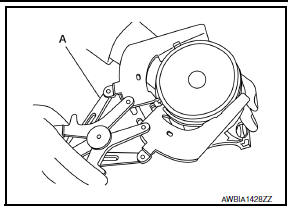
- Remove piston from connecting rod with the following procedure:
- Using snap ring pliers (A), remove snap rings.
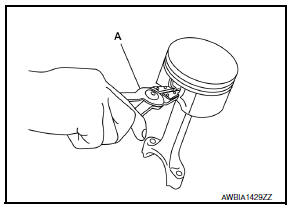
- Heat piston to 60 to 70В°C (140 to 158В°F) with a heat gun (A).
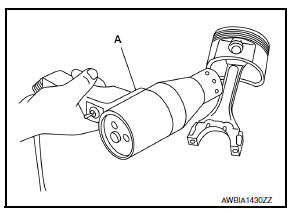
- Push out piston pin using a punch of outer diameter
approximately
18 mm (0.71 in).
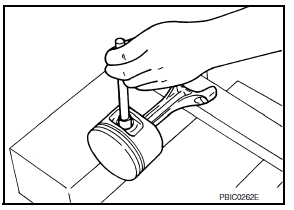
- Remove main bearing cap bolts.
- Measure crankshaft end play before loosening main bearing cap bolts.
Refer to EM-103, "Inspection".
- Loosen and remove main bearing cap bolts in reverse order
as shown.
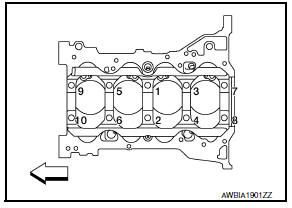
- Remove main bearing caps.
- Tap main bearing caps lightly with a plastic hammer for removal. Number
main bearing caps so they can
be assembled in the same position and direction.
CAUTION:
Do not damage the mounting surface.
- Remove crankshaft.
CAUTION:
- Do not damage or deform signal plate (1) mounted on rear
end of crankshaft (A).
- When setting crankshaft on a flat floor surface, use a
block of wood to avoid interference between signal plate
and the floor surface.
- Do not remove signal plate unless it is necessary to do
so.
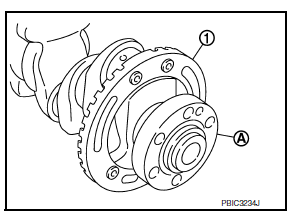
- Remove main bearings and thrust bearings from cylinder block and main
bearing caps.
CAUTION:
When removing them, note the installation position. Keep them in the
correct order.
ASSEMBLY
CAUTION:
Do not reuse washers.
- Fully air-blow engine coolant and engine oil passages in cylinder block,
cylinder bore and crankcase to
remove any foreign material.
CAUTION:
Use goggles to protect your eyes.
- Install each plug to cylinder block as shown.
(2) : Washer
- Apply liquid gasket to the thread of water drain plug (4).
Use Genuine Silicone RTV Sealant, or equivalent. Refer to
GI-21, "Recommended Chemical Products and Sealants".
- Apply sealant to the thread of plug (1).
Use Genuine Silicone RTV Sealant, or equivalent. Refer to
GI-21, "Recommended Chemical Products and Sealants".
NOTE:
Do not apply liquid gasket or high strength thread locking sealant to the
plug (3).
- Tighten each plug as specified below.
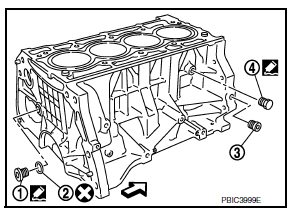

- Install main bearings and thrust bearings with the following procedure:
- Remove dust, dirt, and engine oil on the bearing mating surfaces of
cylinder block and main bearing cap.
- Install thrust bearings to both sides of the No. 3 journal housing
(B) on cylinder block.
- Install thrust bearings with the oil groove (A) facing crankshaft
arm (outside).
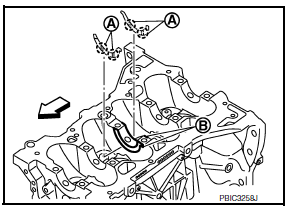
- Install the main bearings paying attention to the direction.
- Before installing main bearings, apply new engine oil to the bearing
surface (inside). Do not apply new
engine oil to the back surface, but thoroughly clean it.
- When installing, align main bearing to the center position of cylinder
block and main bearing cap.
- The difference (A) between main bearing (upper) (1) and main
bearing (lower) (3) should be 0.85 mm (0.0335 in) or less
when installing.
(2) : Cylinder block
(4) : Main bearing cap
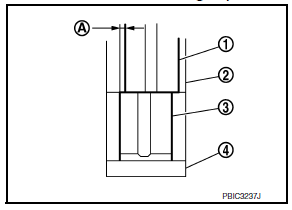
- Ensure the oil holes on cylinder block and oil holes (A) on the
main bearings (1) are aligned.
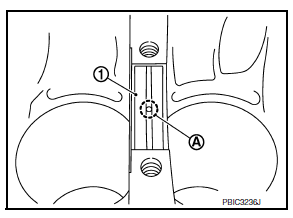
- Install signal plate to crankshaft if removed.
- Set the signal plate with the flange facing toward the counter weight
side (engine front side) to the crankshaft
rear surface.
- Apply new engine oil to threads and seat surfaces of bolts.
- Position crankshaft (2) and signal plate (1) using a dowel pin,
and tighten bolts in numerical order as shown.
(A) : Dowel pin hole
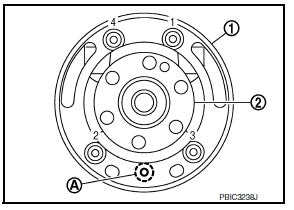
NOTE:
Dowel pin of crankshaft and signal plate is provided as a set for
each.
- Remove dowel pin.
CAUTION:
Be sure to remove dowel pin.
- Install crankshaft to cylinder block.
- While turning crankshaft by hand, check that it turns smoothly.
- Install main bearing caps with the following procedure:
- Install main bearing caps referring to the journal No. stamp (A)
and front mark (B) as shown.
NOTE:
Main bearing cap cannot be replaced as a single part, because it
is machined together with cylinder block.
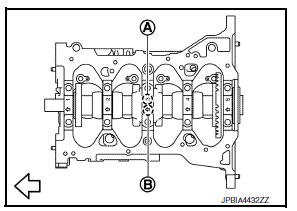
- Tighten main bearing cap bolts in numerical order as shown.
- Apply new engine oil to threads and seat surfaces of bolts.
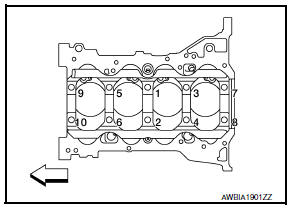
CAUTION:
Confirm the tightening angle by using Tool (A). Do not
judge by visual inspection without the tool.
Step 1 : 34.3 NВ·m (3.5 kg-m, 25 ft-lb)
Step 2 : 60В° clockwise in numerical order
Tool number : KV10112100 (BT-8653-A)
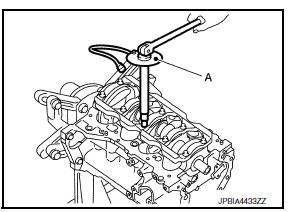
- After installing bolts, check that crankshaft can be rotated smoothly by
hand.
- Check crankshaft end play. Refer to EM-103, "Inspection".
- Install piston to connecting rod with the following procedure:
- Using snap ring pliers, install new snap ring to the groove of the
piston rear side.
- Insert it fully into groove to install.
- Assemble piston to connecting rod.
- Using a heat gun, heat the piston until the piston pin can be pushed in
by hand without excess force
[approximately 60 to 70В°C (140 to 158В°F)]. From the front to the rear,
insert piston pin into piston and
connecting rod.
- Assemble so that the front mark (A) on the piston head and
the oil hole (B) and the cylinder number (D) on connecting rod
are positioned as shown.
(C) : Engine type
(E) : Large end hole diameter grade
(F) : Front mark (connecting rod)
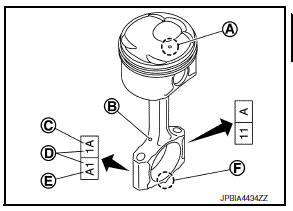
- Install new snap ring to the groove of the piston front side.
- Insert it fully into groove to install.
- After installing, check that connecting rod moves smoothly.
CAUTION:
Do not reuse snap rings.
- Using a suitable tool, install piston rings.
CAUTION:
- Do not damage piston.
- Do not damage piston rings by expanding them excessively.
- Position each ring with the gap as shown referring to the piston
front mark.
(A) : Oil ring upper or lower rail gap
(B) : Front mark
(C) : Second ring and oil ring spacer gap
(D) : Top ring gap
(E) : Stamped mark
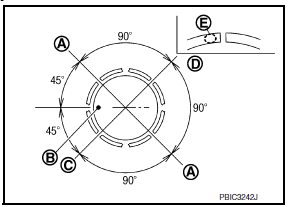
CAUTION:
Do not contact the rail end gap under the oil ring with the
oil drain cast groove of piston.
- Install second ring with the stamped surface facing upward.
- Install connecting rod bearing upper (2) and lower (3) to connecting
rod (4) and connecting rod cap (4).
(C) : Oil hole (connecting rod)
(D) : View D
(E) : OK
(F) : NG
(g) : 2.55 - 2.95 mm (0.1004 - 0.1161 in)
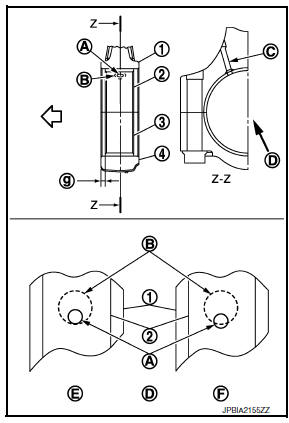
- Install the connecting rod in the direction shown.
- Check that connecting rod bearing oil hole (A) is completely in
the inside of connecting rod oil hole chamfered area (B).
- When installing connecting rod bearings, apply new engine oil
to the bearing surface (inside). Do not apply new engine oil to
the back surface, but thoroughly clean it.
NOTE:
- There is no positioning tab.
- Install the connecting rod bearings in the center of connecting
rod and connecting rod cap as shown. For service operation,
the center position can be checked, visually.
- Install piston and connecting rod assembly to crankshaft.
- Position crankshaft pin corresponding to connecting rod to be installed
onto the bottom dead center.
- Apply new engine oil sufficiently to the cylinder bore, piston and
crankshaft pin.
- Match the cylinder position with the cylinder number (D) on
connecting rod to install.
(A) : Front mark (piston)
(B) : Oil hole
(C) : Engine type
(E) : Large end hole diameter grade
(F) : Front mark (connecting rod)
- Install so that front mark (A) on the piston head faces the front
of engine.
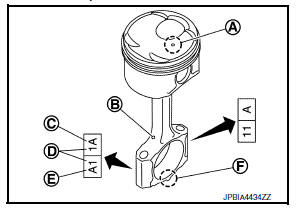
- Install piston with the front mark on the piston head facing the
front of the engine using Tool (A).
CAUTION:
Be careful not to damage the crankshaft pin, resulting
from an interference of the connecting rod big end.
Tool number : EM03470000 (J-8037)
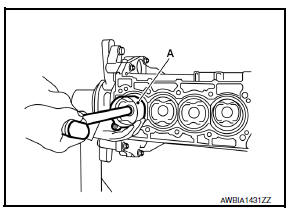
- Install connecting rod cap.
- Match the stamped cylinder number marks (D) on connecting
rod with those on connecting rod cap to install.
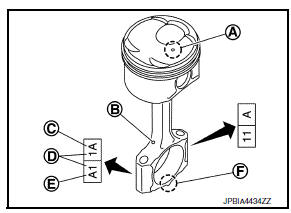
(A) : Front mark (piston)
(B) : Oil hole
(C) : Engine type
(E) : Large end hole diameter grade
(F) : Front mark (connecting rod)
- Tighten connecting rod cap bolt using Tool (A) as follows: Apply new
engine oil to the threads and seats of
connecting rod cap bolts.
Tool number : KV10112100 (BT-8653-A)
CAUTION:
- Check that there is no gap in the thrust surface (A) of the
joint between connecting rod (1) and connecting rod cap
(2) and that these parts are in the correct position. And
then, tighten the connecting rod cap bolts.
- If the connecting rod cap bolts are reused, measure the
outer diameter. Refer to EM-103, "Inspection".
Step 1 : 19.6 NВ·m (2.0 kg-m, 14 ft-lb)
Step 2 : 65В° clockwise
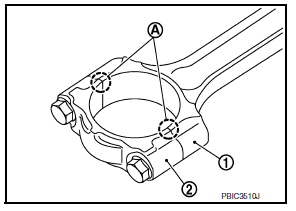
CAUTION:
Check and confirm the tightening angle by using Tool. Do
not judge by visual inspection without the tool.
Tool number : KV10112100 (BT-8653-A)
- After tightening connecting rod cap bolt, check that crankshaft
rotates smoothly.
- Check the connecting rod side clearance. Refer to EM-103,
"Inspection".
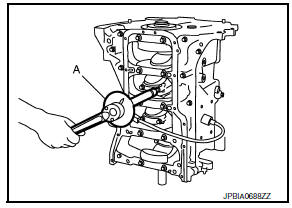
- Install oil pan (upper). Refer to EM-33, "Exploded View".
- Install rear oil seal. Refer to EM-70, "REAR OIL SEAL : Removal and
Installation".
- Install flywheel or drive plate. Refer to EM-90, "Removal and
Installation" (M/T) or EM-92, "Removal and
Installation" (CVT).
- Install knock sensor.
- Install knock sensor (1) with harness connector facing toward
the rear of engine.
(A) : Cylinder block left side
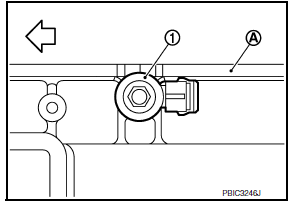
CAUTION:
- Do not tighten bolts while holding the harness connector.
- If any impact by dropping is applied to knock sensor,
replace it with a new one.
NOTE:
- Check that there is no foreign material on the cylinder block
mating surface and the back surface of knock sensor.
- Check that knock sensor does not interfere with other parts.
- Assembly is in the reverse order of disassembly.
Inspection
CRANKSHAFT END PLAY
- Measure the clearance between thrust bearings and crankshaft
arm when crankshaft is moved fully forward or backward using
suitable tool (A).
Standard and Limit : Refer to EM-123, "Cylinder
Block".
- If the measured value exceeds the limit, replace thrust bearings,
and measure again. If it still exceeds the limit, replace crankshaft
also.
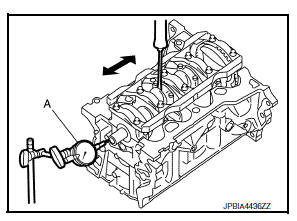
Connecting rod side clearance
- Measure the side clearance between connecting rod and crankshaft
arm using suitable tool (A).
Standard and Limit : Refer to EM-123, "Cylinder
Block".
- If the measured value exceeds the limit, replace connecting rod,
and measure again. If it still exceeds the limit, replace crankshaft
also.
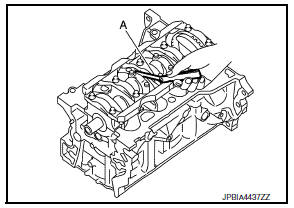
Piston to piston pin oil clearance
Piston Pin Hole Diameter
Measure the inner diameter of piston pin hole using suitable tool (A).
Standard : Refer to EM-123, "Cylinder Block".
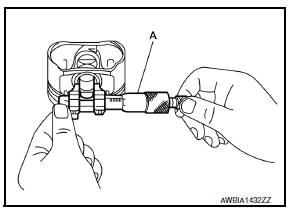
Piston Pin Outer Diameter
Measure the outer diameter of piston pin using suitable tool (A).
Standard : Refer to EM-123, "Cylinder Block".
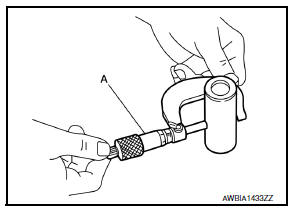
Piston to Piston Pin Oil Clearance
(Piston to piston pin oil clearance) = (Piston pin hole diameter) – (Piston
pin outer diameter)
Standard : Refer to EM-123, "Cylinder Block".
- If oil clearance is out of the standard, replace piston and piston pin
assembly.
- When replacing piston and piston pin assembly. Refer to EM-112, "Description".
NOTE:
- Piston is available together with piston pin as assembly.
- Piston pin (piston pin hole) grade is provided only for the parts
installed at the plant. For service parts, no
grades can be selected. (Only grade “0” is available.)
Piston ring side clearance
- Measure the side clearance of piston ring and piston ring groove
using suitable tool (A).
Standard and Limit : Refer to EM-123, "Cylinder
Block".
- If the measured value exceeds the limit, replace piston ring, and
measure again. If it still exceeds the limit, replace piston also.
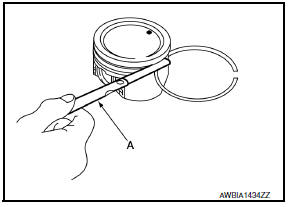
Piston ring end Gap
- Check that cylinder bore inner diameter is within specification. Refer
to “PISTON TO CYLINDER BORE
CLEARANCE”.
- Lubricate with new engine oil to piston (1) and piston ring (2), and
then insert (A) piston ring until middle of cylinder (B) with piston,
and measure piston ring end gap using suitable tool (C).
Standard and Limit : Refer to EM-123, "Cylinder
Block".
- If the measured value exceeds the limit, replace piston ring, and
measure again. If it still exceeds the limit, rebore cylinder and use
oversized piston and piston rings.
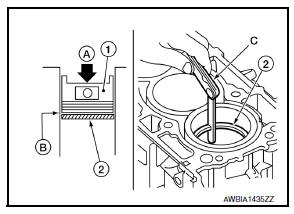
Connecting rod bend and torsion
- Check with a connecting rod aligner.
(A) : Bend
(B) : Torsion
(C) : Feeler gauge
Limit : Refer to EM-123, "Cylinder Block".
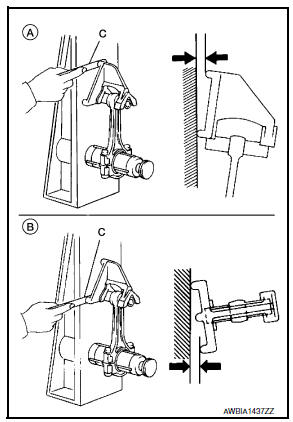
- If it exceeds the limit, replace connecting rod assembly.
Connecting rod big end diameter
- Install connecting rod cap (1) without connecting rod bearing
installed, and tightening connecting rod cap bolts to the specified
torque. Refer to EM-95, "Disassembly and Assembly".
(2) : Connecting rod
(A) : Example
(B) : Measuring direction of inner diameter
- Measure the inner diameter of connecting rod big end using suitable
tool.
Standard : Refer to EM-123, "Cylinder Block".
- If out of the standard, replace connecting rod assembly.
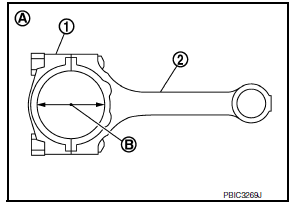
Connecting rod bushing oil clearance
Connecting Rod Bushing Inner Diameter
Measure the inner diameter of connecting rod bushing using suitable
tool (A).
Standard : Refer to EM-123, "Cylinder Block".
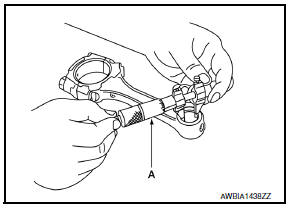
Piston Pin Outer Diameter
Measure the outer diameter of piston pin using suitable tool (A).
Standard : Refer to EM-123, "Cylinder Block".
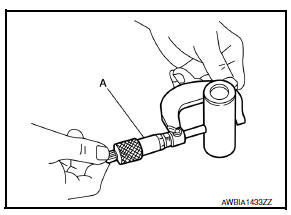
Connecting Rod Bushing Oil Clearance
(Connecting rod bushing oil clearance) = (Connecting rod bushing inner
diameter) – (Piston pin outer diameter)
Standard and Limit : Refer to EM-123, "Cylinder Block".
- If the measured value is out of the standard, replace connecting rod
assembly and/or piston and piston pin
assembly.
- If replacing piston and piston pin assembly. Refer to EM-112, "Piston".
- If replacing connecting rod assembly. Refer to EM-113, "Connecting Rod
Bearing".
Cylinder block top surface distortion
Using a scraper, remove gasket on the cylinder block surface, and also remove
engine oil, scale, carbon, or
other contamination.
CAUTION:
Be careful not to allow gasket flakes to enter engine oil or engine
coolant passages.
- Measure the distortion on the cylinder block upper face at some
different points in six directions using suitable tools (A,B).
Limit : Refer to EM-123, "Cylinder Block".
If it exceeds the limit, replace cylinder block.
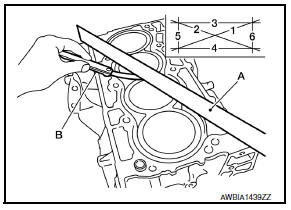
Main bearing housing inner diameter
- Install main bearing cap without main bearings installed, and tighten
main bearing cap bolts to the specified
torque. Refer to EM-95, "Disassembly and Assembly".
- Measure the inner diameter of main bearing housing using suitable tool.
- Measure the position shown [5 mm (0.20 in)] backward from main
bearing housing front side in the 2 directions as shown. The
smaller one is the measured value.
(1) : Cylinder block
(2) : Main bearing cap
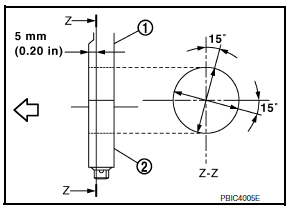
Standard : Refer to EM-123, "Cylinder Block".
- If out of the standard, replace cylinder block and main bearing
caps assembly
NOTE:
Main bearing cap cannot be replaced as a single part, because it is
machined together with cylinder block
Piston to cylinder bore clearance
Cylinder Bore Inner Diameter
- Measure the cylinder bore for wear, out-of-round and taper at six
different points on each cylinder using suitable tool. [(A) and (B)
directions at (C), (D), and (E)] [(A) is in longitudinal direction of
engine]
(f) : 10 mm (0.39 in)
(g) : 60 mm (2.36 in)
(h) : 130 mm (5.12 in)
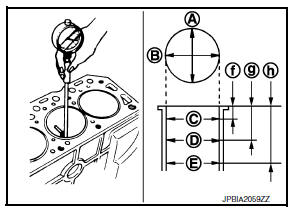
NOTE:
When determining cylinder bore grade, measure the cylinder bore
(B) direction at (D) position.
Standard:
Cylinder bore inner diameter
: Refer to EM-123, "Cylinder Block".
Limit:
Out-of-round [Difference between (A) and (B)]
Taper [Difference between (C) and (D)]
: Refer to EM-123, "Cylinder Block".
- If the measured value exceeds the limit, or if there are scratches
and/or seizure on the cylinder inner wall,
replace cylinder block.
NOTE:
Oversize piston is not provided.
Piston Skirt Diameter
Measure the outer diameter of piston skirt using suitable tool (A).
Standard : Refer to EM-123, "Cylinder Block".
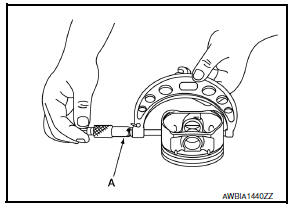
Piston to Cylinder Bore Clearance
Calculate by piston skirt diameter and cylinder bore inner diameter
[direction (B), position (D)].
(A) : Direction A
(C) : Position C
(E) : Position E
(f) : 10 mm (0.39 in)
(g) : 60 mm (2.36 in)
(h) : 130 mm (5.12 in)
(Clearance) = (Cylinder bore inner diameter) – (Piston skirt diameter)
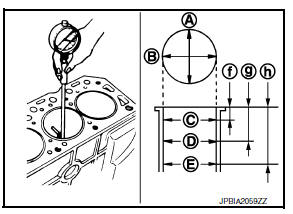
Standard and Limit : Refer to EM-123, "Cylinder Block".
- If it exceeds the limit, replace piston and piston pin assembly and/or
cylinder block. Refer to EM-112, "Piston".
Crankshaft main journal diameter
- Measure the outer diameter of crankshaft main journals using suitable
tool (A).
Standard : Refer to EM-123, "Cylinder Block".
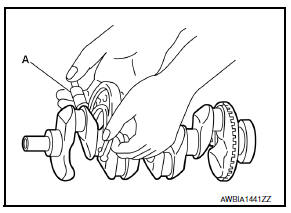
Crankshaft pin journal diameter
- Measure the outer diameter of crankshaft pin journal using suitable
tool.
Standard : Refer to EM-123, "Cylinder Block".
- If out of the standard, measure the connecting rod bearing oil
clearance. Then use undersize bearing. Refer
to EM-127, "Connecting Rod Bearing".
Out-of-round and taper of crankshaft
- Measure the dimensions at four different points as shown on each
main journal and pin journal using suitable tool.
- Out-of-round is indicated by the difference in dimensions between
(X) and (Y) at (A) and (B).
- Taper is indicated by the difference in dimension between (A) and
(B) at (X) and (Y).
Limit:
Out-of-round [Difference between (X) and (Y)]
Taper [Difference between (A) and (B)]
: Refer to EM-123, "Cylinder Block".
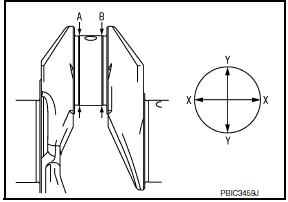
- If the measured value exceeds the limit, correct or replace crankshaft.
- If corrected, measure the bearing oil clearance of the corrected main
journal and/or pin journal. Then select
main bearing and/or connecting rod bearing. Refer to EM-113, "Connecting Rod
Bearing" and/or EM-115,
"Main Bearing".
Crankshaft runout
- Place a v-block on a precise flat table to support the journals on both
ends of the crankshaft.
- Place a suitable tool (a) straight up on the no. 3 Journal.
- While rotating crankshaft, read the movement of the pointer on the
suitable tool (a). (Total indicator reading)
Standard and limit : refer to em-123, "cylinder
block".
- If it exceeds the limit, replace crankshaft.
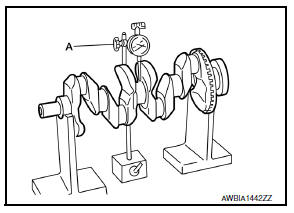
Connecting rod bearing oil clearance
Method by Calculation
- Install connecting rod bearings (2) to connecting rod (3) and connecting
rod bearing cap (1), and tighten connecting rod cap bolts to
the specified torque. Refer to EM-95, "Disassembly and Assembly".
(A) : Example
(B) : Inner diameter measuring direction
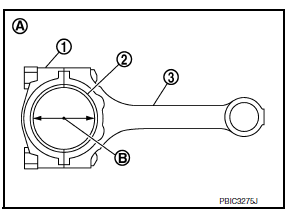
Standard and Limit : Refer to EM-127, "Connecting Rod
Bearing".
- If clearance exceeds the limit, select proper connecting rod bearing
according to connecting rod big end
diameter and crankshaft pin journal diameter to obtain specified bearing oil
clearance. Refer to EM-113,
"Connecting Rod Bearing".
Method of Using Plastigage
- Remove engine oil and dust on crankshaft pin and the surfaces of each
bearing completely.
- Cut a plastigage slightly shorter than the bearing width, and place it
in crankshaft axial direction, avoiding oil
holes.
- Install connecting rod bearings to connecting rod and cap, and tighten
connecting rod cap bolts to the specified
torque. Refer to EM-95, "Disassembly and Assembly".
CAUTION:
Do not rotate crankshaft.
- Remove connecting rod cap and bearing, and using the scale (A)
on the plastigage bag, measure the plastigage width.
NOTE:
The procedure when the measured value exceeds the limit is
same as that described in the “Method by Calculation”.
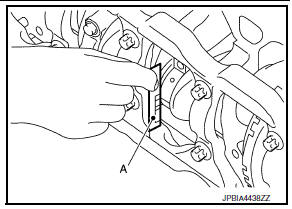
Main bearing oil clearance
Method by Calculation
(A) : Example
(B) : Inner diameter measuring direction
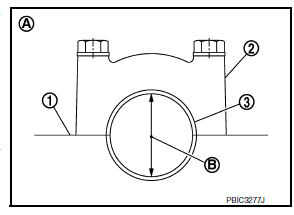
Standard and Limit : Refer to EM-127, "Main Bearing".
- If clearance exceeds the limit, select proper main bearing according to
main bearing inner diameter and
crankshaft main journal diameter to obtain specified bearing oil clearance.
Refer to EM-115, "Main Bearing".
Method of Using Plastigage
- Remove engine oil and dust on crankshaft main journal and the surfaces
of each bearing completely.
- Cut a plastigage slightly shorter than the bearing width, and place it
in crankshaft axial direction, avoiding oil
holes.
- Install main bearings to cylinder block and main bearing cap, and
tighten main bearing cap bolts to the specified
torque. Refer to EM-95, "Disassembly and Assembly".
CAUTION:
Do not rotate crankshaft.
- Remove main bearing cap and bearings, and using the scale (A)
on the plastigage bag, measure the plastigage width.
NOTE:
The procedure when the measured value exceeds the limit is the
same as that described in the “Method by Calculation”.
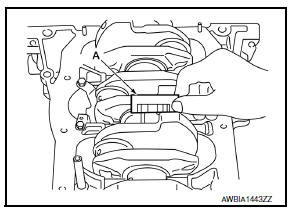
Main bearing crush height
- When main bearing cap is removed after being tightened to the
specified torque with main bearings (1) installed, the tip end of
bearing must protrude (B). Refer to EM-95, "Disassembly and
Assembly".
(A) : Example
Standard : There must be crush height.
- If the standard is not met, replace main bearings.
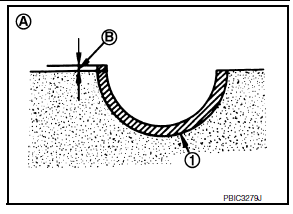
Connecting rod bearing crush height
- When connecting rod cap is removed after being tightened to the
specified torque with connecting rod bearings (1) installed, the tip
end of bearing must protrude (B). Refer to EM-95, "Disassembly
and Assembly".
(A) : Example
Standard : There must be crush height.
- If the standard is not met, replace connecting rod bearings.
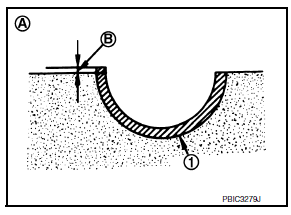
Main bearing cap bolt outer diameter
- Measure the outer diameters (d1) and (d2) at two positions as
shown.
(A) : (d1) measuring position
(B) : (d2) measuring position
- If reduction appears in places other than (b) range, regard it as
(d2).
Limit [(d1) – (d2)]: 0.15 Mm (0.0059 In)
- If it exceeds the limit (a large difference in dimensions), replace
main bearing cap mounting bolt with a new one.
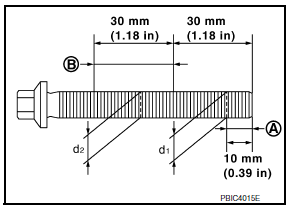
Connecting rod cap bolt outer diameter
- Measure the outer diameter (d) at position as shown.
- If reduction appears in a position other than (d), regard it as (d).
Limit: 7.75 Mm (0.3051 In)
- When (d) exceeds the limit (when it becomes thinner), replace
connecting rod cap bolt with a new one.
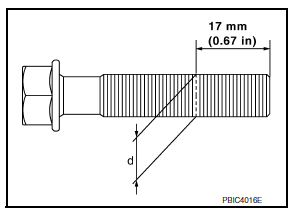
Exploded View
Pilot converter
Drive plate
Reinforcement plate
Chamfered
Removal and Installation
REMOVAL
Remove the engine and the transaxle assembly from the vehicle, and
...
Description
Selection points
Selection parts
Selection items
Selection methods
Between cylinder block and
crankshaft
Main bearing
Main bearing grade (bearing
thi ...
Other materials:
P0461 Fuel level sensor
DTC Logic
DTC DETECTION LOGIC
NOTE:
If DTC P0461 is displayed with DTC UXXXX, first perform the trouble
diagnosis for DTC UXXXX.
If DTC P0461 is displayed with DTC P0607, first perform the trouble
diagnosis for DTC P0607. Refer
to EC-350, "DTC Logic".
Driving long distan ...
The steering switch (meter control switch) is inoperative
Description
If any of the following malfunctions is found for the steering switch (meter
control switch) operation.
All switches are inoperative
The specified switch cannot be operated
Diagnosis procedure
1.Check steering switch signal circuit
Check the steering switch signal circuit. ...
A-bag branch line circuit
Diagnosis procedure
Warning:
Always observe the following items for preventing accidental
activation.
Before servicing, turn ignition switch off, disconnect battery
negative terminal, and wait 3 minutes
or more. (To discharge backup capacitor.)
Never use unspecified tester or other me ...
© 2014-2025 Copyright www.nisentra.com