Nissan Sentra Service Manual: Cylinder head
Exploded View
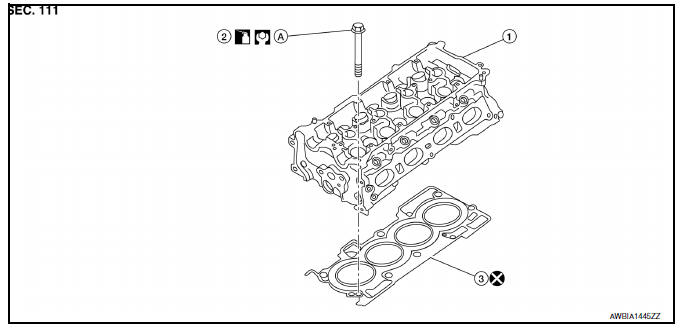
- Cylinder head assembly
- Cylinder head bolt
- Cylinder head gasket
- Refer to INSTALLATION
Removal and Installation
REMOVAL
- Release fuel pressure. Refer to EC-143, "Work Procedure".
- Drain engine coolant and engine oil. Refer to CO-12, "Changing Engine
Coolant" (for Coolant) and LU-8,
"Draining" (for Oil).
- Remove fan motor and shroud assembly. Refer to CO-17, "Component".
- Remove the exhaust manifold. Refer to EM-30, "Exploded View"
- Remove the intake manifold. Refer to EM-27, "Exploded View".
- Remove the fuel injector and fuel tube assembly. Refer to EM-40, "Exploded
View".
- Remove the water outlet. Refer to CO-24, "Exploded View".
- Remove the rocker cover. Refer to EM-46, "Exploded View".
- Remove the front cover and timing chain. Refer to EM-48, "Exploded View".
- Remove the camshaft. Refer to EM-60, "Exploded View".
- Remove cylinder head.
- Loosen cylinder head bolts in the reverse order as shown.
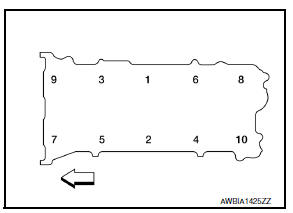
- Remove cylinder head gasket.
INSTALLATION
- Install cylinder head gasket.
CAUTION:
Do not reuse cylinder head gasket.
- Install cylinder head, and tighten cylinder head bolts in order as shown
using Tool (A).
- Clean threads and seating surfaces of bolts.
- Apply new engine oil to threads and seating surface of bolts.
CAUTION:
- If cylinder head bolts are reused, check their outer diameters
before installation. Refer to EM-79,
"Inspection".
- Check and confirm the tightening angle by using Tool. Do
not judge by visual inspection without the tool.
Tool number : KV10112100 (BT-8653-A)
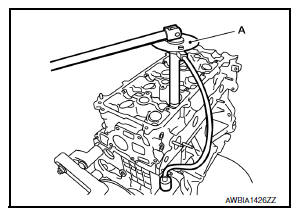
Step 1 : 40.0 NВ·m (4.1 kg-m, 30 ft-lb)
Step 2 : 100В° clockwise in order
Step 3 : 0 NВ·m (0 kg-m, 0 ft-lb)
Step 4 : 40.0 NВ·m (4.1 kg-m, 30 ft-lb)
Step 5 : 100В° clockwise in order
Step 6 : 100В° clockwise in order
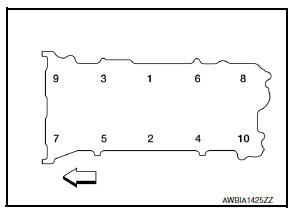
- Installation of remaining components is in the reverse order of removal.
Exploded View
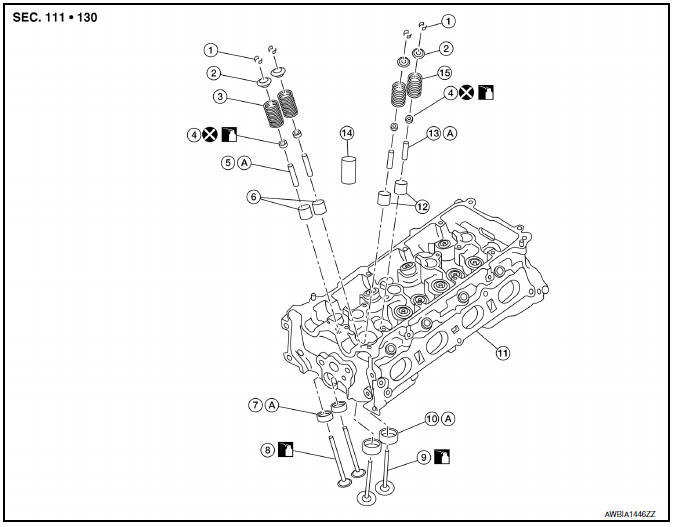
- Valve collet
- Valve spring retainer
- Valve spring (EXH)
(with valve spring seat)
- Valve oil seal
- Valve guide (EXH)
- Valve lifter (EXH)
- Valve seat (EXH)
- Valve (EXH)
- Valve (INT)
- Valve seat (INT)
- Cylinder head
- Valve lifter (INT)
- Valve guide (INT)
- Spark plug tube
- Valve spring (INT)
(with valve spring seat)
- Refer to INSTALLATION
Disassembly and Assembly
DISASSEMBLY
- Remove spark plug using suitable tool.
- Remove valve lifter.
- Identify installation positions, and store them without mixing them up.
- Remove valve collet, valve spring retainer, and valve spring
using Tools.
Tool number (A) : KV1016200 (J-26336-A)
Tool number (B) : KV10109220 ( — )
Tool number (C) : KV10115900 (J-26336-20)
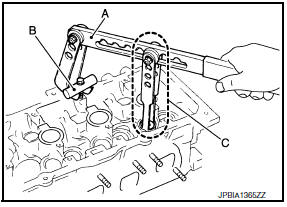
CAUTION:
- Do not damage valve lifter holes.
- Install Tool (A) in the center of valve spring retainer (1) to
install it.
Tool number : KV10115900 (J-26336-20)
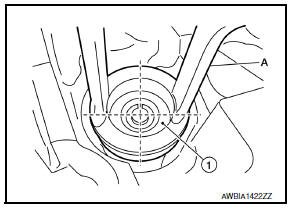
- Remove valve spring retainer and valve spring (with valve spring seat).
CAUTION:
Do not remove valve spring seat from valve spring.
- Push valve stem to combustion chamber side, and remove valve.
- Identify installation positions, and store them without mixing them up.
- Remove valve oil seal using Tool (A).
Tool number : KV10107902 (J-38959)
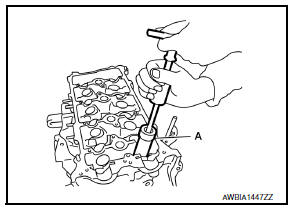
- Remove valve seat, if necessary
- Bore out old seat until it collapses. Boring should not continue beyond
the bottom face of the seat
recess in cylinder head. Set the machine depth stop to ensure this. Refer to
EM-121, "Cylinder Head".
CAUTION:
Do not bore excessively to prevent damage to cylinder head.
- Remove valve guide, if necessary.
- To remove valve guide, heat cylinder head to 110 to 130В°C (230
to 266В°F) by soaking in heated oil (A).
WARNING:
Cylinder head contains heat. When working, wear protective
equipment to avoid getting burned.
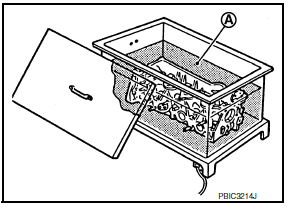
- Drive out valve guide using suitable tool.
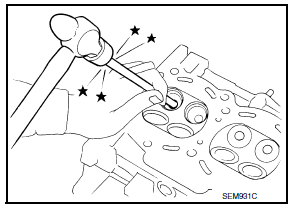
ASSEMBLY
- Install valve guide, if removed.
CAUTION:
Replace with oversize [0.2 mm (0.008 in)] valve guide. Refer to EM-121,
"Cylinder Head".
- Ream cylinder head valve guide hole using suitable tool (A).
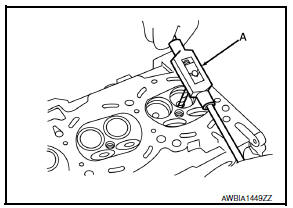
- Heat cylinder head to 110 to 130В°C (230 to 266В°F) by soaking in
heated oil (A).
WARNING:
Cylinder head contains heat. When working, wear protective
equipment to avoid getting burned.
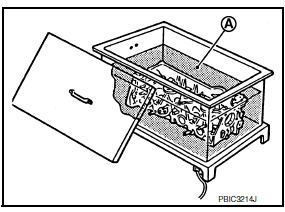
- Press valve guide (1) from camshaft side to dimension as
shown.
(2) : Cylinder head
Projection (H) : Refer to EM-121, "Cylinder Head".
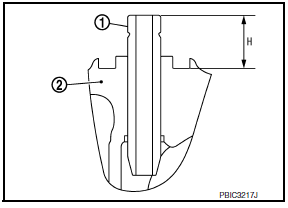
- Apply reamer finish to valve guide using suitable tool (A).
Standard : Refer to EM-121, "Cylinder Head".
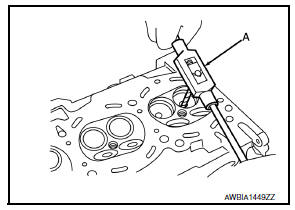
- Install valve seat, if removed.
CAUTION:
Replace with oversize [0.5 mm (0.020 in)] valve seat. Refer to EM-121,
"Cylinder Head".
- Ream cylinder head (1) recess diameter for service valve seat
(2).
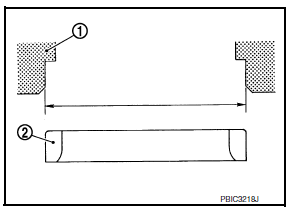
- Heat cylinder head to 110 to 130В°C (230 to 266В°F) by soaking in
heated oil (A).
WARNING:
Cylinder head contains heat. When working, wear protective
equipment to avoid getting burned.
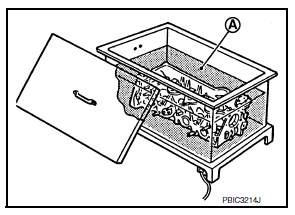
- Provide valve seats cooled well with dry ice. Press-fit valve seat into
cylinder head.
CAUTION:
Do not touch cold valve seats directly.
- Finish valve seat to the specified dimension using suitable tool.
Refer to EM-121, "Cylinder Head".
CAUTION:
When using valve seat cutter, firmly grip the cutter handle
with both hands. Then, press on the contacting surface all
around the circumference to cut in a single drive. Improper
pressure on the cutter or cutting many different times may
result in stage valve seat.
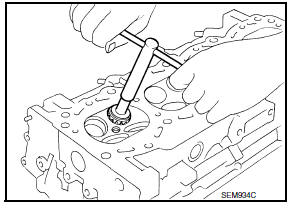
- Using compound, grind to adjust valve.
- Check again for normal contact. Refer to EM-121, "Cylinder
Head".
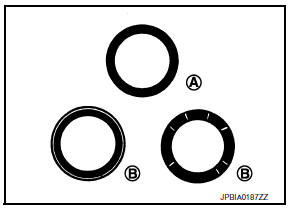
- Install valve oil seal using Tool (A).
NOTE:
Dimension is height measured before installing valve spring
(with valve spring seat).
Height (H) : 15.1 - 15.7 mm (0.594 - 0.618 in)
Tool number : KV10115600 (J-38958)
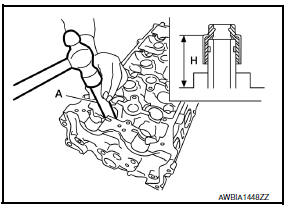
- Install valve.
- Install larger diameter to intake side.
- Install valve spring with valve spring seat (1) (do not remove from
valve spring).
- Install smaller pitch (valve spring seat side) to cylinder head
side (B).
- Confirm identification color (A) of valve spring.
Intake : White
Exhaust : Orange
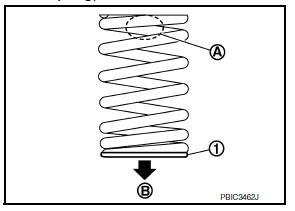
- Install valve spring retainer.
- Install valve collet.
- Compress valve spring using Tool. Install valve collet with a
magnet hand.
Tool number (A) : KV1016200 (J-26336-A)
Tool number (B) : KV10109220 ( — )
Tool number (C) : KV10115900 (J-26336-20)
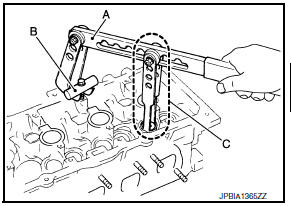
CAUTION:
When working do not damage valve lifter holes.
- Tap valve stem edge lightly with a plastic hammer after installation
to check its installed condition.
- Install valve lifter.
- Install it in the original position.
- Install spark plug. Refer to EM-12, "Exploded View".
Inspection
INSPECTION AFTER REMOVAL
Cylinder Head Bolts Outer Diameter
- Cylinder head bolts are tightened by plastic zone tightening
method. Whenever the size difference between (d1) and (d2)
exceeds the limit, replace them with a new one.
Limit [(d1) – (d2)]: 0.15 mm (0.0059 in)
- If reduction of outer diameter appears in a position other than (d2),
use it as (d2) point.
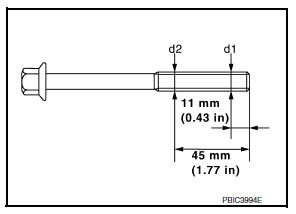
Cylinder Head Distortion
NOTE:
When performing this inspection, cylinder block distortion should also be
checked. Refer to EM-123, "Cylinder
Block".
- Wipe off engine oil and remove water scale (like deposit), gasket,
sealant, carbon, etc. with a scraper.
CAUTION:
Do not allow gasket debris to enter passages for engine oil or water.
- At each of several locations on bottom surface of cylinder head,
measure the distortion in six directions using suitable tools (A,
B).
Limit: Refer to EM-121, "Cylinder Head".
- If it exceeds the limit, replace cylinder head.
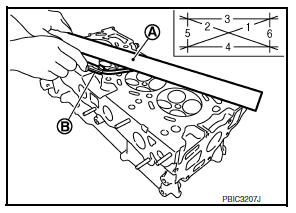
INSPECTION AFTER DISASSEMBLY
Valve Dimensions
- Check the dimensions of each valve. Refer to EM-121, "Cylinder Head".
- If dimensions are out of the standard, replace valve and check valve
seat contact. Refer to “VALVE SEAT
CONTACT”.
Valve Guide Clearance
Valve Stem Diameter
- Measure the diameter of valve stem using suitable tool (A).
Standard: Refer to EM-121, "Cylinder Head".
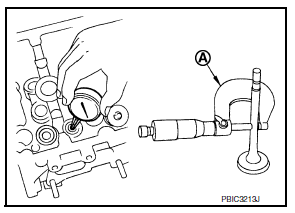
Valve Guide Inner Diameter
- Measure the inner diameter of valve guide using suitable tool.
Standard: Refer to EM-121, "Cylinder Head".
Valve Guide Clearance
- (Valve guide clearance) = (Valve guide inner diameter) – (Valve
stem diameter)
Standard and Limit: Refer to EM-121, "Cylinder Head".
- If the calculated value exceeds the limit, replace valve and/or valve
guide, when valve guide must be
replaced. Refer to EM-74, "Disassembly and Assembly".
Valve Seat Contact
- After confirming that the dimensions of valve guides and valves are
within the specifications, perform this
procedure.
- Apply prussian blue (or white lead) onto contacting surface of valve
seat to check the condition of the valve
contact on the surface.
- Check if the contact area band is continuous all around the
circumference.
(A) : OK
- If not, grind to adjust valve fitting and check again. If the contacting
surface still has “NG” conditions (B) even after the recheck,
replace valve seat. Refer to EM-74, "Disassembly and Assembly".
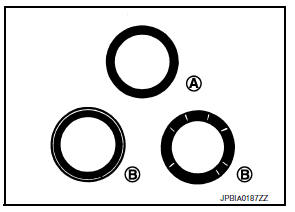
VALVE SPRING SQUARENESS
- Set a try square (A) along the side of valve spring and rotate
spring. Measure the maximum clearance between the top of spring
and try square.
(B) : Contact
Limit : Refer to EM-121, "Cylinder Head".
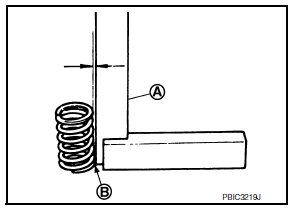
VALVE SPRING DIMENSIONS AND VALVE SPRING PRESSURE LOAD
- Check valve spring pressure with valve spring seat installed at the
specified spring height.
CAUTION:
Do not remove valve spring seat from valve spring.
Standard : Refer to EM-121, "Cylinder Head".
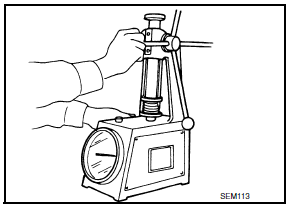
- If the installation load or load with valve open is out of the standard,
replace valve spring (with valve spring seat).
INSPECTION AFTER INSTALLATION
- Before starting engine, check oil/fluid levels including engine coolant
and engine oil. If less than required
quantity, fill to the specified level. Refer to MA-11, "Fluids and
Lubricants".
- Use procedure below to check for fuel leakage.
- Turn ignition switch “ON” (with engine stopped). With fuel pressure
applied to fuel piping, check for fuel leakage
at connection points.
- Start engine. With engine speed increased, check again for fuel leakage
at connection points.
- Run engine to check for unusual noise and vibration.
NOTE:
If hydraulic pressure inside timing chain tensioner drops after removal
and installation, slack in the guide
may generate a pounding noise during and just after engine start. However, this
is normal. Noise will stop
after hydraulic pressure rises.
- Warm up engine thoroughly to check there is no leakage of fuel, exhaust
gases, or any oil/fluids including
engine oil and engine coolant.
- Bleed air from lines and hoses of applicable lines, such as in cooling
system.
- After cooling down engine, again check oil/fluid levels including engine
oil and engine coolant. Refill to the
specified level, if necessary.
- Summary of the inspection items:
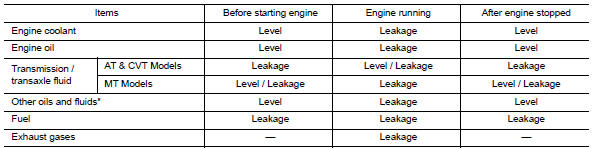
*: Power steering fluid, brake fluid, etc.
Valve oil seal : Removal and Installation
REMOVAL
Rotate crankshaft, and set piston whose valve oil seal is to be removed
to TDC. This will prevent valve
from dropping into cylinder.
CAUT ...
Other materials:
Dtc/circuit diagnosis
Power supply and ground circuit
Audio unit
Audio unit : diagnosis procedure
Regarding Wiring Diagram information, refer to AV-157, "Wiring Diagram".
1.Check fuse
Are the fuses blown?
Yes >> replace the blown fuse after repairing the affected circuit.
No >> go to 2.
...
Precautions in repairing high strength steel
High strength steel (HSS)
High strength steel is used for body panels in order to reduce vehicle
weight.
Accordingly, precautions in repairing automotive bodies made of high strength
steel are described below:
Tensile strength
Nissan/Infiniti designation
Major applicable parts
...
Clutch piping
Exploded View
CSC (Concentric Slave Cylinder)
Clip
Clutch tube
Clutch damper
Bracket
Clutch master cylinder
Hydraulic Layout
Clutch tube
Lock pin
CSC (Concentric Slave Cylinder)
Clutch damper
Clutch master cylinder
Clutch pedal
Removal and Installation
CAU ...
© 2014-2025 Copyright www.nisentra.com